4 Mistakes to Avoid in Refractory Repairs | Precast Refractory Shapes
Common Refractory Mistakes
Selecting and installing a proper refractory lining for your application can be complicated. Picking the wrong refractory material or installing it incorrectly can lead to premature failure, making you less productive and costing you more money than you planned to spend. Here are four common mistakes that must be avoided when making refractory repairs:
1.Thinking that all refractory materials are the same and can be used for any application: Refractory materials have a wide range of physical properties, and are designed for specific purposes. Materials should be carefully selected for each application. There are often trade-offs in physical properties (insulating capability vs strength, for instance), which must be considered.
2.
Improper anchoring:
Providing the correct anchoring system is just as important as material selection in the design of a durable refractory lining. Improper anchor spacing, selecting the wrong anchor type, or having the wrong anchor metallurgy can all lead to the premature failure of a refractory lining.
3.Thinking that “anyone can put this stuff in”: Refractory installation requires special know-how, experience, and expertise. Your installers should be skilled in multiple methods of refractory installation to prevent any issues.
4.
Implementing the wrong mixing process:
The proper placement of refractory castables requires close attention to details. Common mistakes include using too much water, using the wrong type of mixer, not allowing the cast material to set properly, and not following initial dry out.
Don’t let these common and avoidable mistakes happen to you. To speak to the refractory experts,
give TFL a call today!
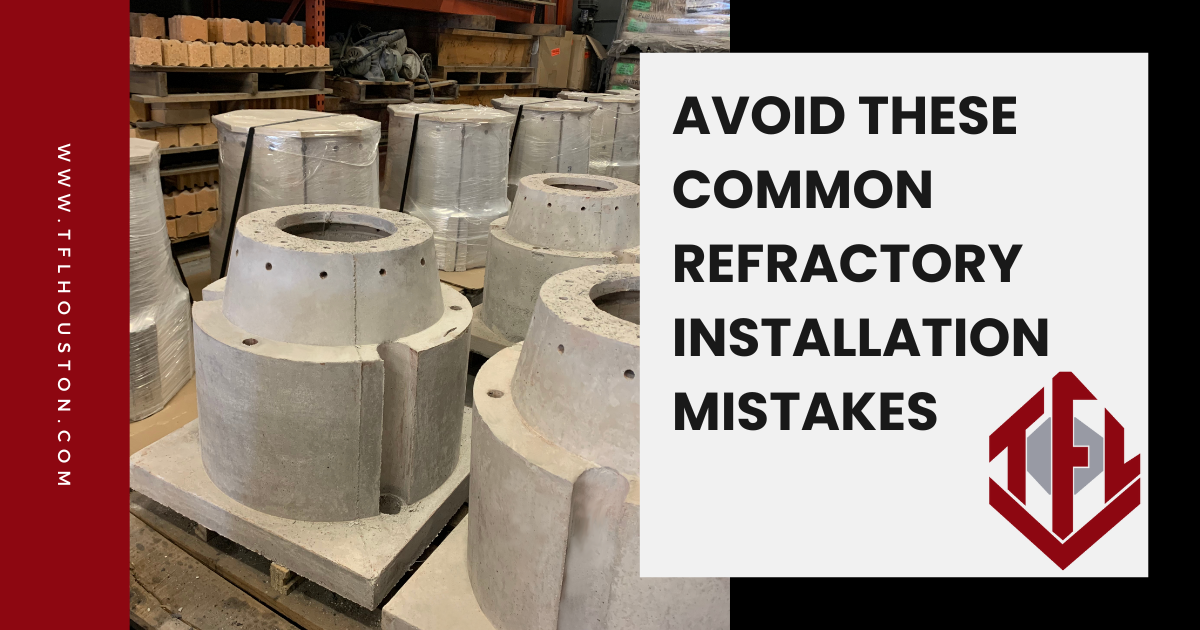
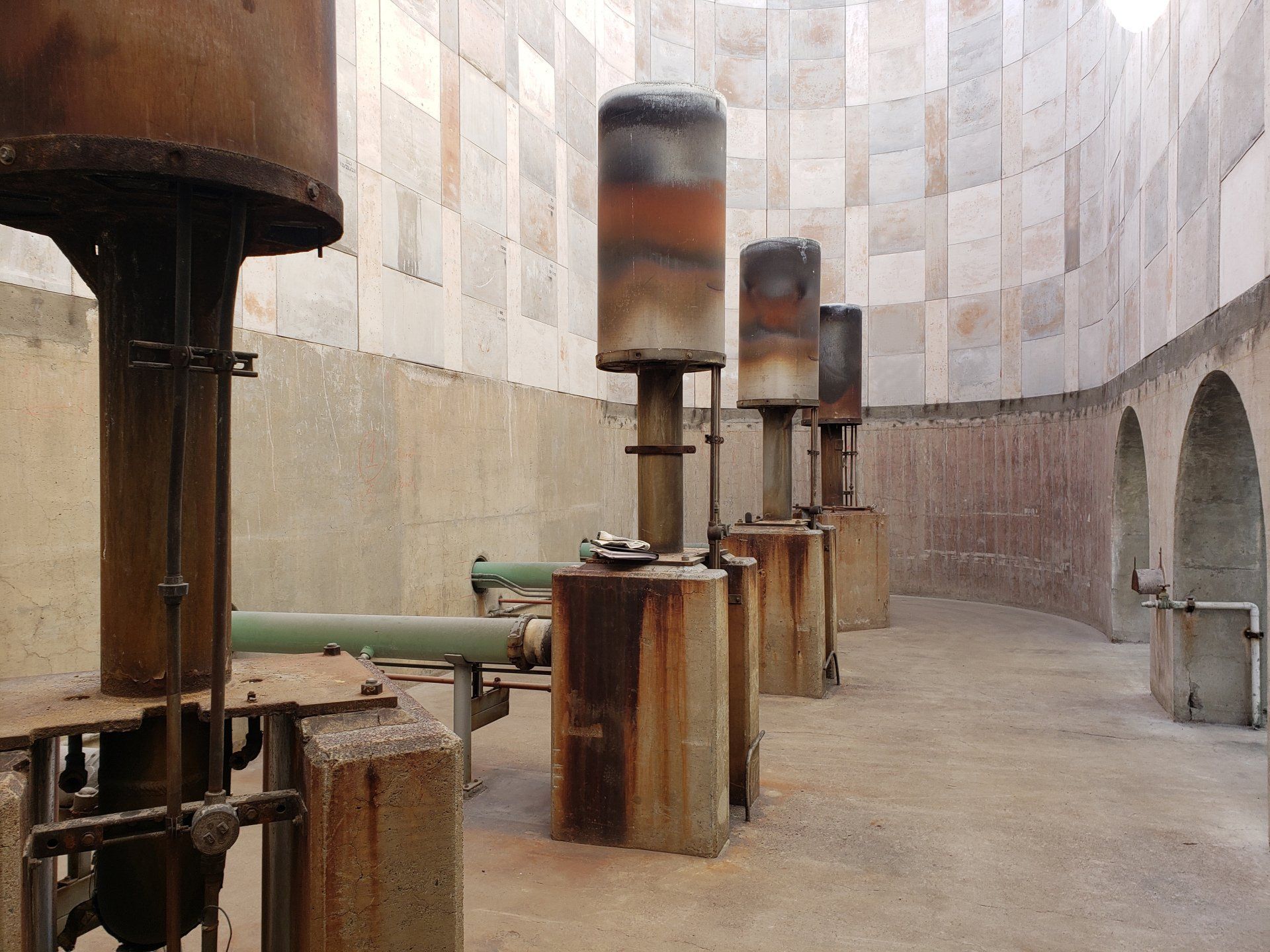
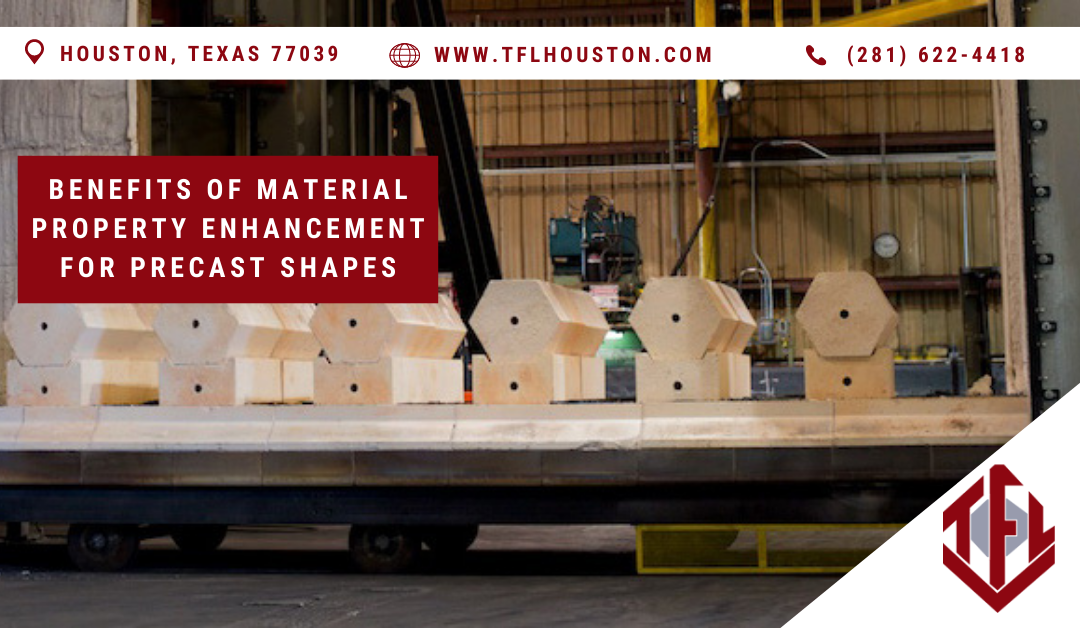
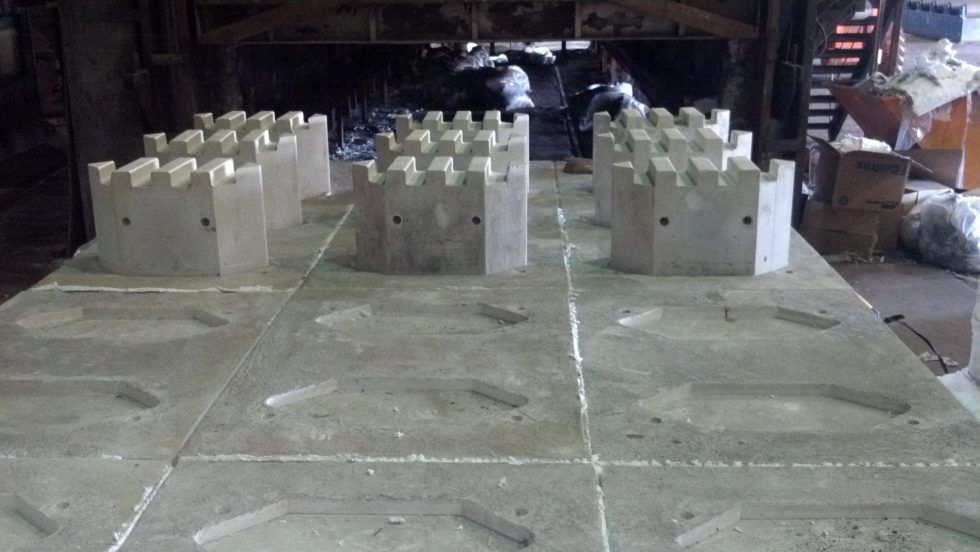
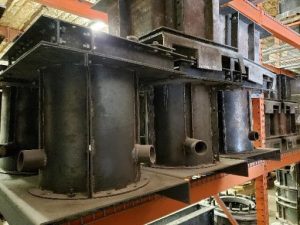
TFL Uses Custom Molding Techniques to Make Precast Refractory Shapes With Extremely Tight Tolerances
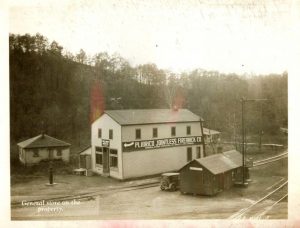
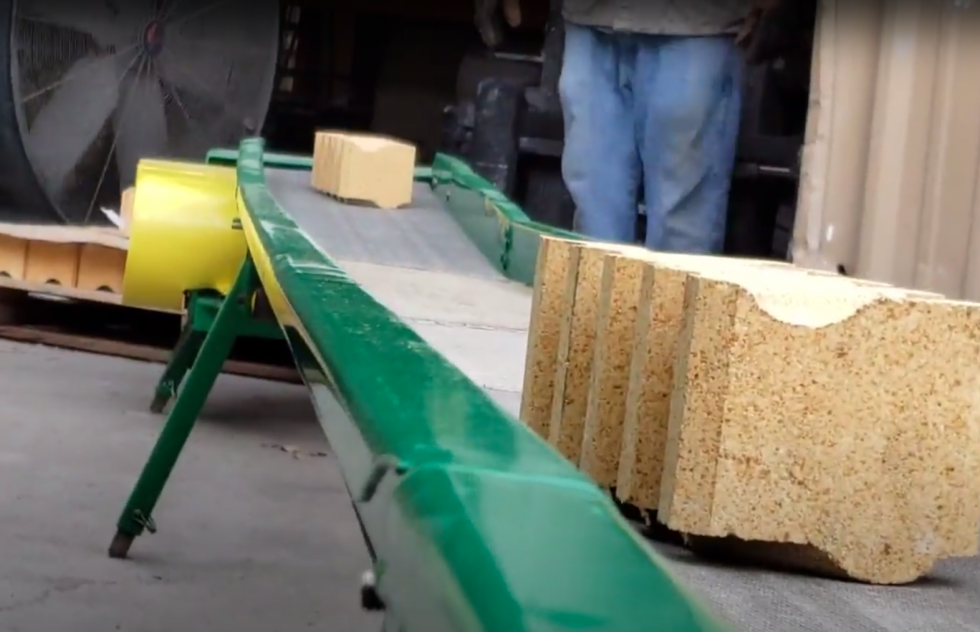