Choosing the Correct Refractory Vendor
When looking at multiple refractory vendors do your research
Not all refractory vendors are created equal. Cheapest isn’t always best when considering the
implications of an abrupt breakdown. You can avoid the agony of unexpected failures that can stop your
production line cold by knowing how to cut through the vendor rhetoric and stay focused on your end
goals.
Single source vs. components
Buying piecemeal components from multiple vendors may appear to save time and money:
● you must work with multiple vendors on everything from billing to delivery
● your components may not all be compatible with one another
● you lose system accountability
● you don’t have a single source when something goes wrong
Category and Industry knowledge
When looking at multiple vendors, do your research and find out how much they know about their industry and yours. Remember, your vendor should be an expert in their field first; the ideal ones are also well-versed in working in your field. Since every application is unique, expertise in direct or adjacent fields helps ensure you get advice you can trust.
Satisfied Customers
Although everyone can pull out a decent customer reference or two, ask your vendor for permission to speak to a couple of clients. A potential vendor with satisfied clients who will rave about the vendor’s services and are willing to talk to you about it is likely to be a vendor you can rely on to help you through any unexpected issues. Also, check out how the vendor addresses emergencies. Are they available 24/7? What can you expect from them when you face an unexpected challenge?
Quality of Materials Produced
If you’re looking at a few vendor options, browse their product spec sheets to look for any differences that may make them stand out. Higher-quality materials typically have higher ratings and tolerance levels. Look at the product lines they represent. Are they well-known and trusted?
How TFL supports industrial refractory needs
For over 40 years, TFL has offered its industrial customers a broad range of high-quality refractory products. TFL specializes in the manufacture of precast refractory shapes systems. We supply high-quality refractory materials and anchoring systems produced by leading U. S. manufacturers. We can also provide customized steel fabrication and shop linings, and our Convey-It system is a very useful tool for the efficient handling of refractory materials.
Contact TFL today to learn more.
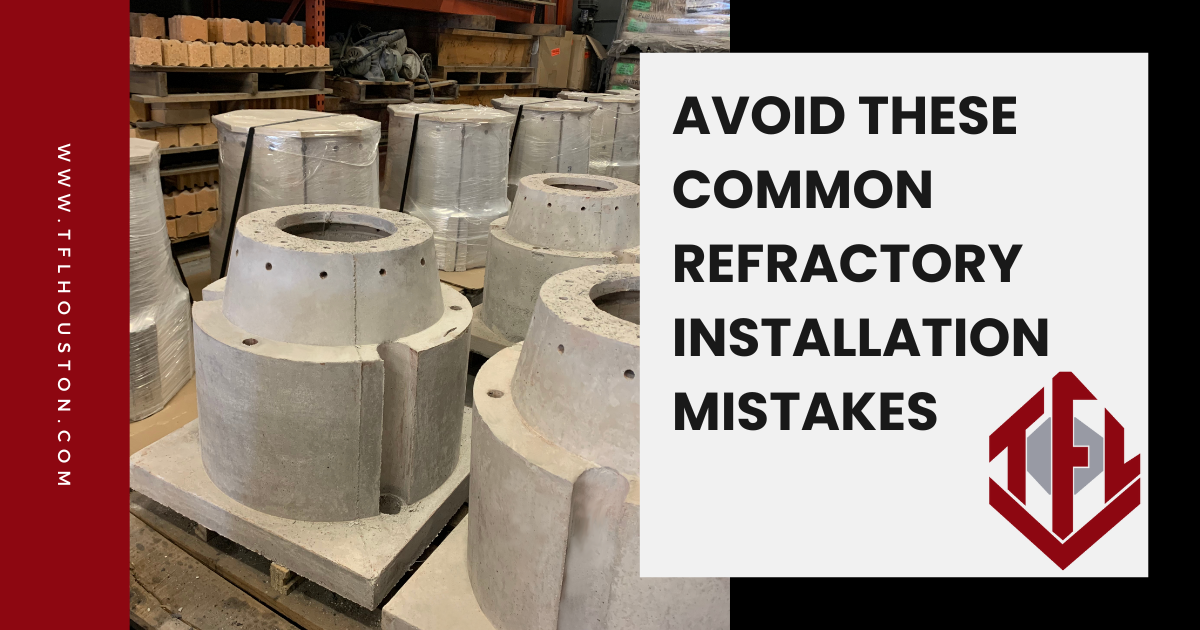
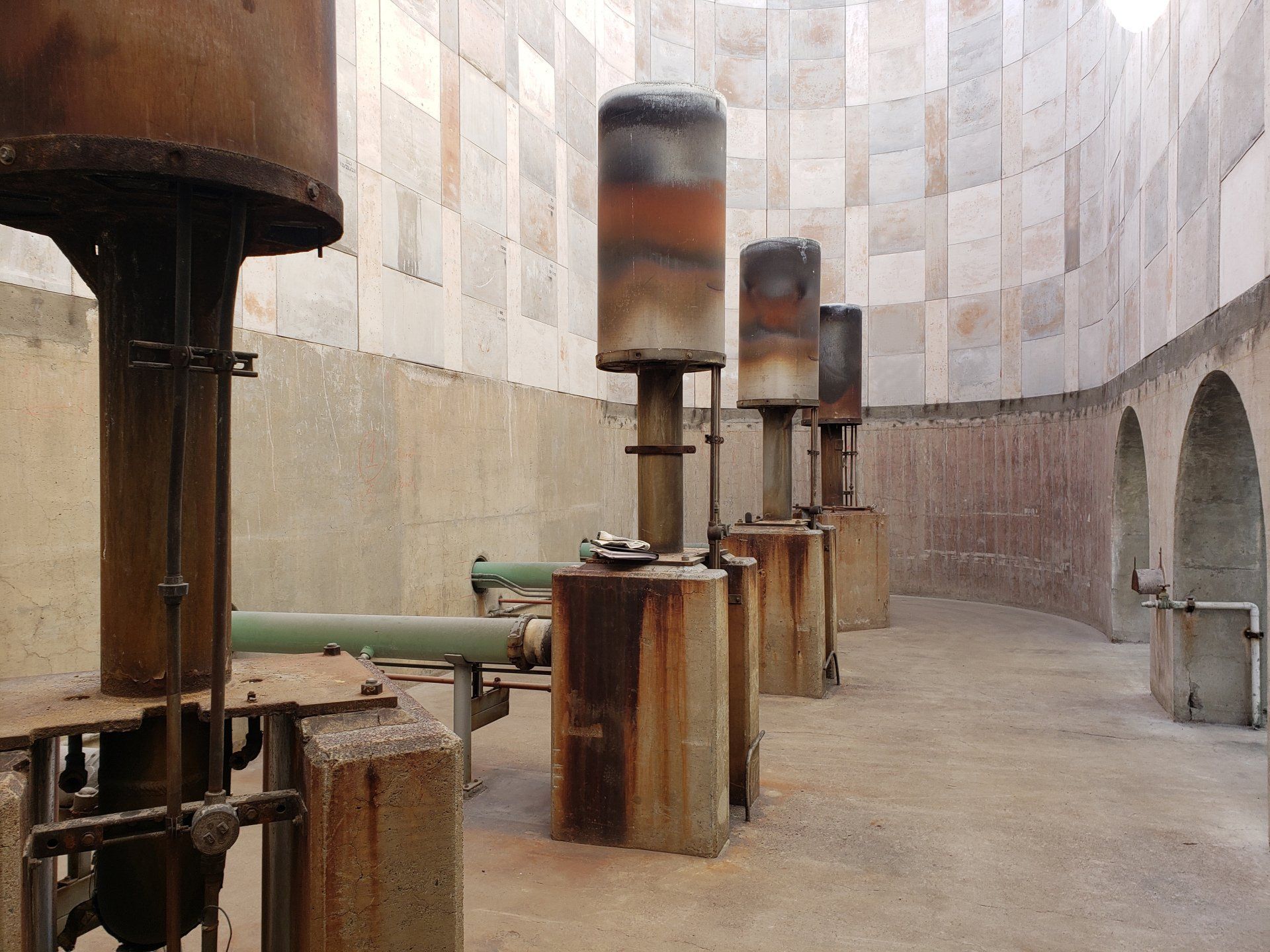
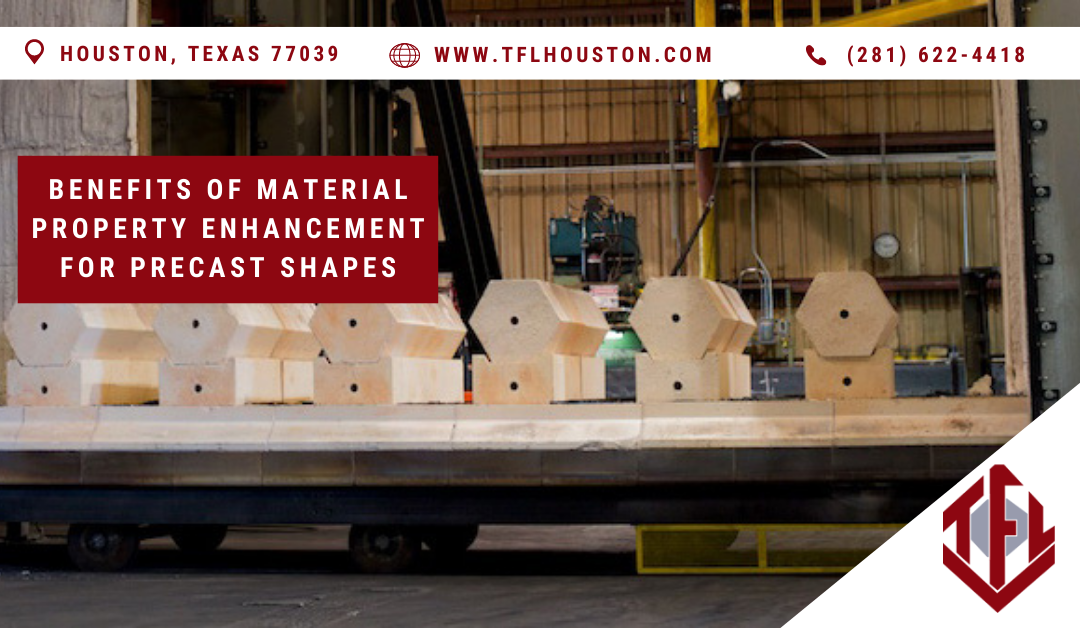
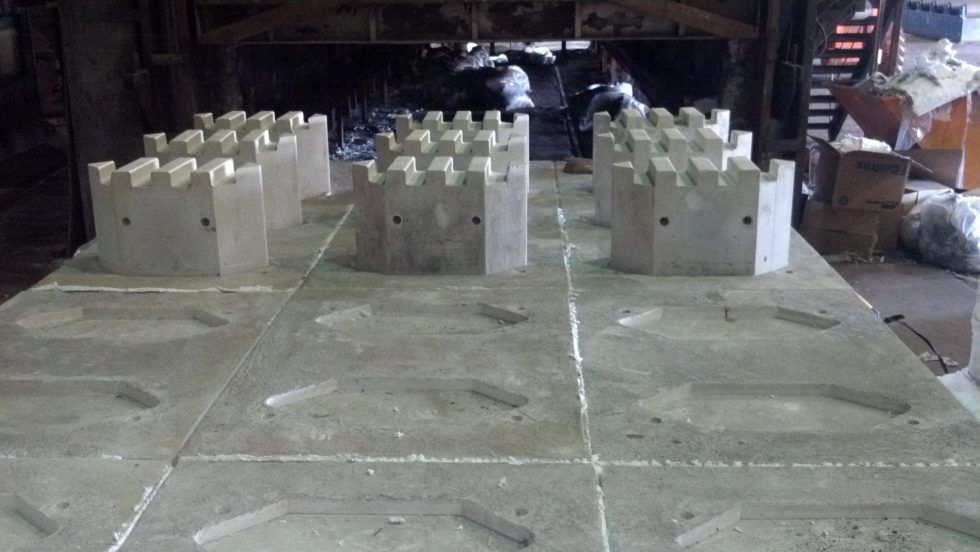
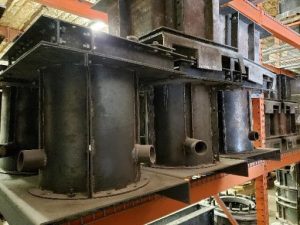
TFL Uses Custom Molding Techniques to Make Precast Refractory Shapes With Extremely Tight Tolerances
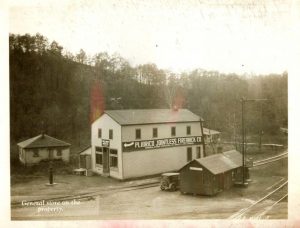
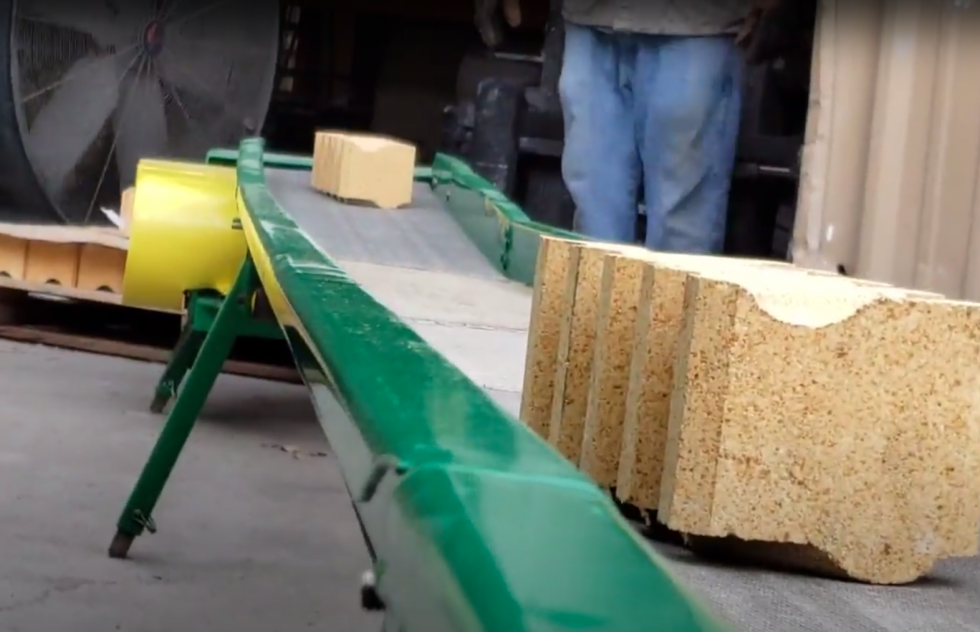