10 Characteristics of Refractories Every Plant Manager Should Know
Refractory materials play an integral role in many industrial heat processes, from glass manufacturing to steel and aluminum production. As a plant manager, you’re not expected to understand the nuances of this complex material, but it’s helpful to know some basic principles and characteristics.
As a plant manager, you should be familiar with some common refractory material traits. Brush up on your knowledge to ensure when the time comes for a repair, you are well equipped to make a decision. #TFL #TFLHouston
Click To Tweet
Characteristics of Refractories
Refractories face an enormous amount of stress in operation. High temperatures are just one of many factors they must weather. Here are 10 common traits of refractory materials:
- Abrasion resistance
- Bulk density
- Cold crushing strength
- Creep
- Melting point
- Porosity
- Pyrometric cone equivalent
- Refractoriness under load
- Stability
- Thermal conductivity
1) Abrasion resistance
Refractory bricks and precast shapes face a number of stressors and must be resistant to more than just pressure. The attacks by gases and fine dust particles result in wear, and the rate of wear is the material’s abrasion resistance, contributing to the life of the refractory.
2) Bulk density
The bulk density (BD) is a measure of the weight of a given volume including the pore space of the refractory. It is one of the most important characteristics and provides a good general indication of product quality.
3) Cold compressive strength
In furnaces, cold compressive strength (CCS) is a measure of the mechanical strength of the refractory shapes. Refractories with high compressive strength are more resistant to impact from rods or slag penetration than shapes with a low CCS.
4) Creep
Refractory material must maintain dimensional stability under extreme temperatures and constant corrosion from hot liquid and gases. Creep (thermal expansion under load) is a property which determines the physical change over time and at a given temperature by a refractory in service.
5) Melting point
Melting point gauges the ability of refractory materials to withstand high temperatures without chemical change or physical destruction.
6) Porosity
Porosity measures the open pore space in the refractory and is expressed as the average percentage of open pore space in the volume of the refractory. With respect to porosity, an important factor is its behavior during an extreme chemical attack by molten metal, slag, fluxes and vapors that can penetrate and contribute to refractory degradation.
Pro Tip: High porosity refractory materials tend to be better insulated because of the high volume of air it traps.
7) Pyrometric cone equivalent
PCE is a quality control method that detects variations in batch chemistry. Pyrometric cone equivalent is the ability to withstand exposure to elevated temperature without undergoing notable deformation. Due to their chemical complexity, refractories melt over a range of temperatures. In this test, ceramic specimens of known softening behavior (Seger or Orton cones) are compared with the cone of the refractory after firing. This ensures consistency and measures refractoriness.
8) Refractoriness under load
Refractoriness under load (RUL) evaluates the softening behavior of fired refractory bricks at rising temperature and constant load conditions. It gives a forecast of the temperature at which the brick will collapse in service condition with a similar load.
9) Stability, Expansion, and Shrinkage at High Temperature
This is the permanent change in the dimension of the refractory due to contraction and expansion in service. Applying extremely high temperatures followed by cooling often creates a permanent change in dimensions. This may cause loosening or destruction of bricks during service.
10) Thermal conductivity
Thermal conductivity is defined as the quantity of heat that will flow through a unit area in a direction normal to the surface area in a defined time with a known temperature gradient under steady state conditions. It indicates general heat flow characteristics of the refractory and depends upon the chemical and mineralogical composition as well as the application temperature. High thermal conductivity refractories are needed for some applications such as coke ovens, regenerators etc, while refractories with lower thermal conductivity are preferred in most applications since they help conserve heat.
Extending the Life of Your Refractory
The refractory material used in your industrial plant play a critical yet often overlooked role in your daily operations. Familiarizing yourself with the general concepts and properties of refractories will only benefit your decision making when the time comes for repairs.
Contact Us to learn more about selecting the right kind of refractory material for your application.
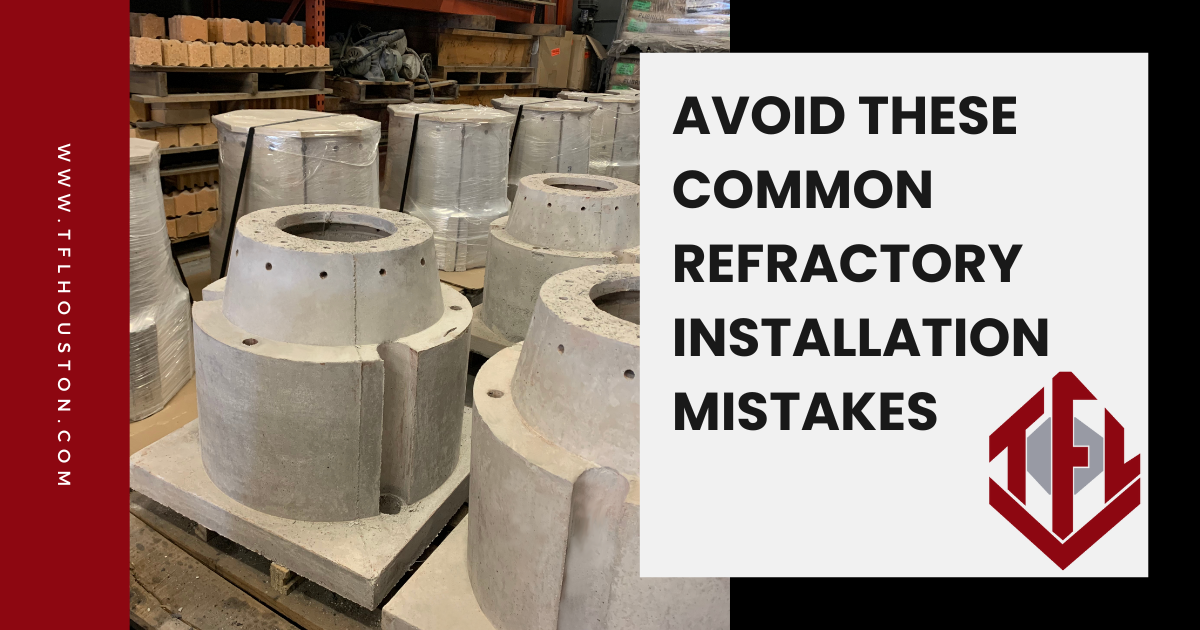
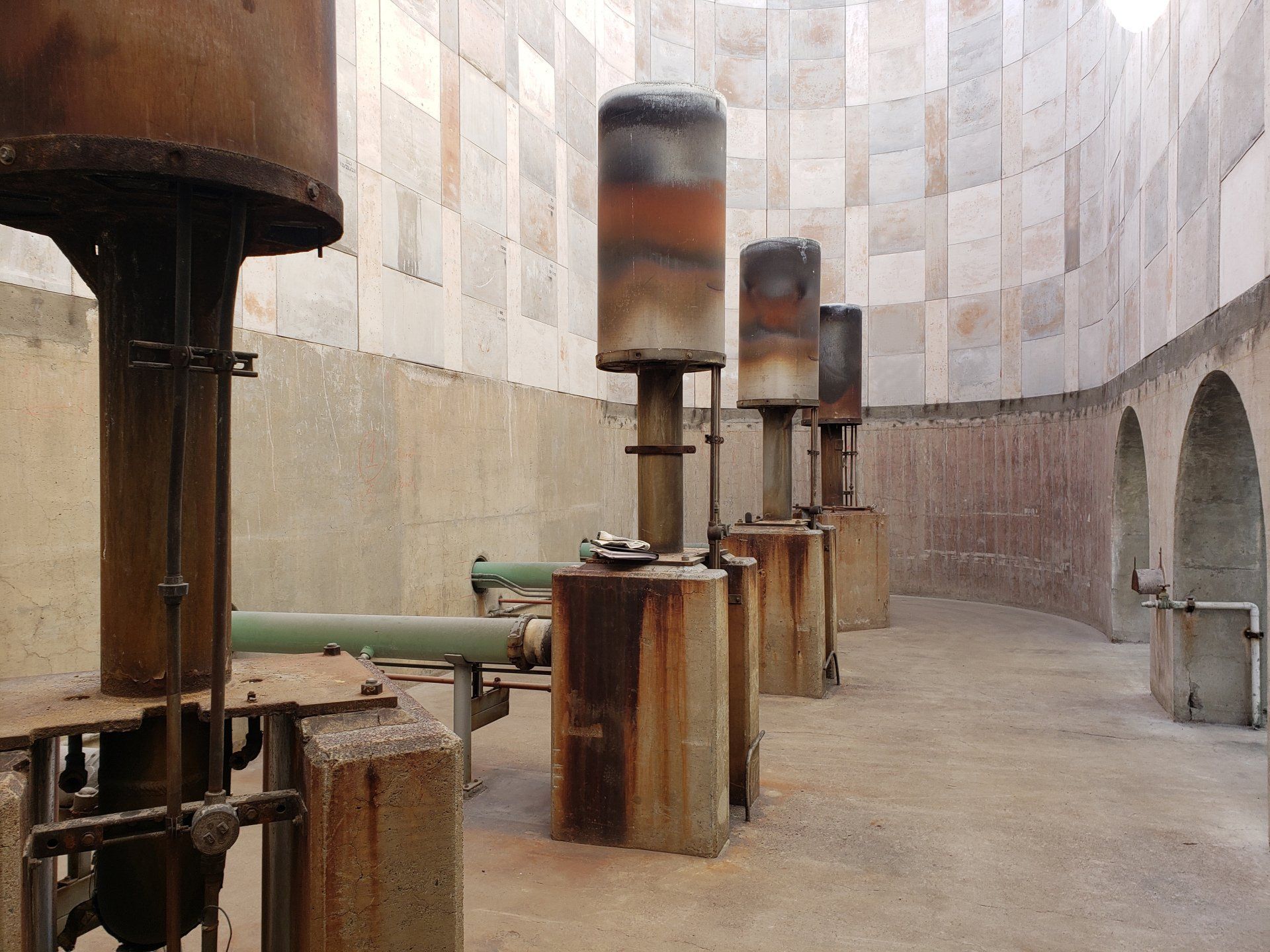
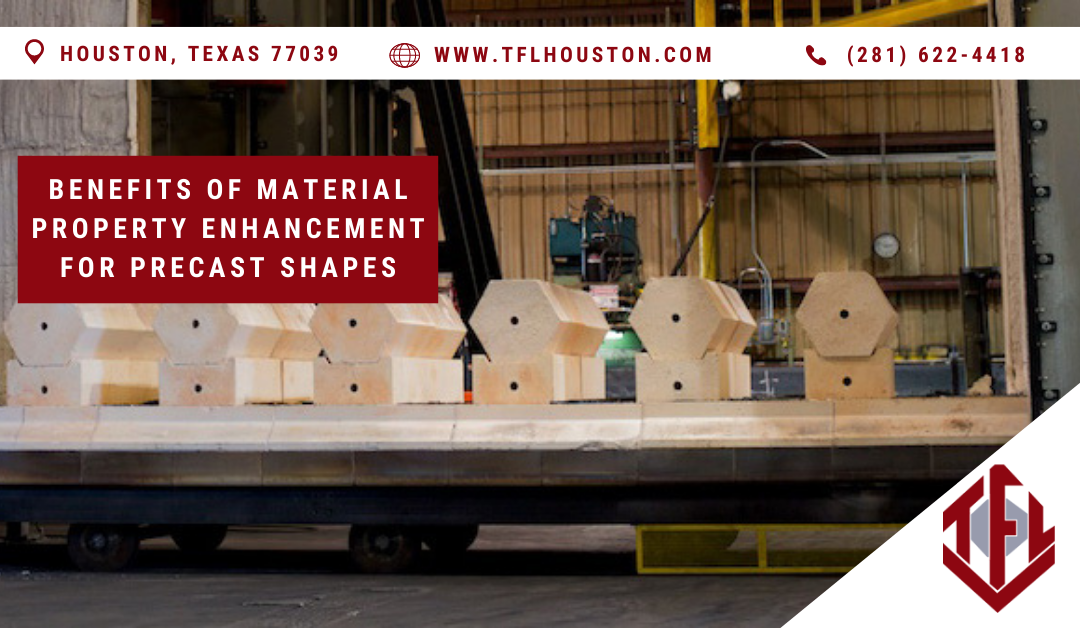
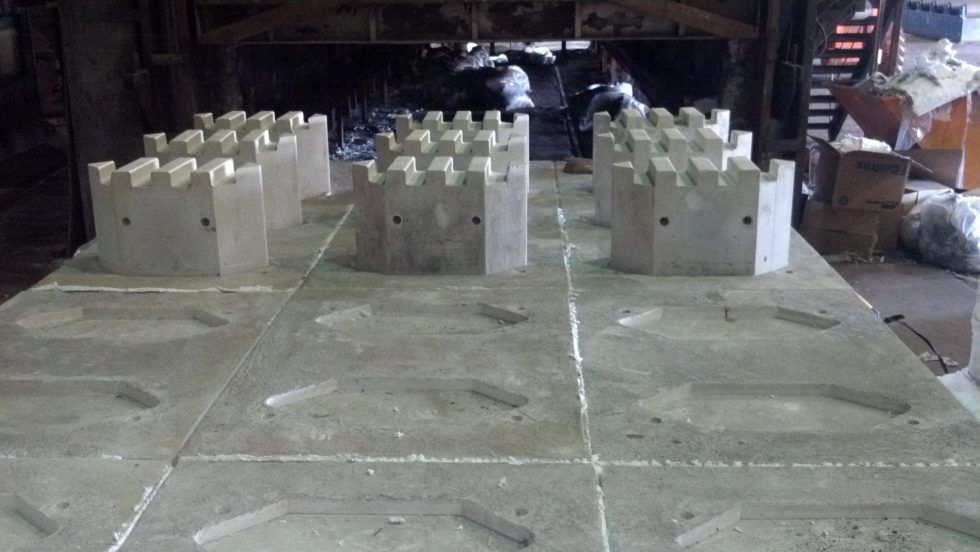
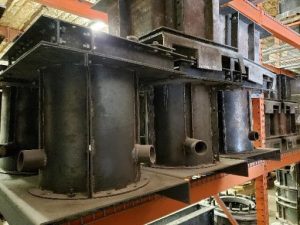
TFL Uses Custom Molding Techniques to Make Precast Refractory Shapes With Extremely Tight Tolerances
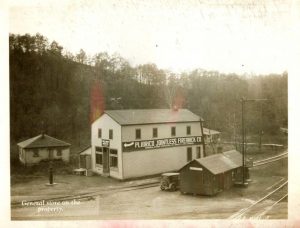