A Brief History of Refractories
Refractories are used in countless industries, from iron and steel to energy and glass. Manufacturing in its current form could not exist if not for the technological advancements in refractory materials since the Industrial Revolution.
A Simple Start
Because of their chemical composition and reactions, refractories are fairly complex. However, the basic principles behind them are remarkably simple. In fact, those principles were present as early as 3000 BC, when people began to dig primitive pit kilns in the ground to fire their earthenware (bowls, plates, etc.)
Iron Age
Refractory technology began in earnest during the Iron Age (2000 BC). Using charcoal in a furnace, iron was produced by reducing the iron ore with extreme heat. Furnaces used in iron production featured very elementary refractory lining, usually consisting of unshaped fireclay, carbon-added composite materials, and silica rock, although blocks cut from natural stones or fireclay brick were also used.
Industrial Revolution
During the 18th and 19th century, refractory technology took great strides. Many industries began using the new technology, prompting a label of the “smokestack industries” for the looming smokestack billowing smoke into the air. The driving force behind the growth was the steel industry. Furnaces used for iron and steel manufacturing during this time had the following characteristics:
- Coke-fed blast furnace: Used coke instead of coal as the reducing agent and heat source.
- Hot stove: Using regenerative heat exchangers to supply heated air to the blast furnace
- Coke oven: Carbonized coal into coke
- Open hearth furnace: Used gas instead of coal, and regenerative heat exchangers, allowing it to utilize its own waste heat.
- Converter: Steelmaking furnace to burn impurities in molten iron with air blown in from the bottom.
New Refractory Technology
While steelmaking was transforming the firing process, refractories were making great advancements, including:
- In 1878 Sidney Gilchrist Thomas and his cousin Percy Gilchrist discovered that phosphorus could be removed from steel melted in a dolomite-lined Bessemer converter.
- Tar-Dolomite brick made the basic (Thomas) converter viable, while silica brick made the acidic (Bessemer) converter and open hearth furnace commercially operational.
- Diatomaceous brick was developed as the first lining material for heat insulation
The 20th Century
In 1901 US Steel was founded as the world’s largest steel manufacturer, and in 1902 Harbison Walker Refractories opened as the largest refractory manufacturer. Thus, the USA was the center of steel manufacturing in the world. Even interrupted by several wars, advancements in refractory technology in this time included:
- Many new types of unshaped refractories and non-oxide materials were developed.
- Refractories were developed for use in other industries, such as the electro-fused cast brick for the glass industry and silicon carbide brick for pottery firing.
- Testing methods for refractories became standardized, with new findings featured in scientific journals.
Post-WWII
Following the second world war, refractory technology continued to be refined and improved upon. The high-pressure, high-temperature blast furnace became widely used, and the performance of various types of refractories became more clear, and material designs were altered to facilitate greater efficiency. Other innovations included:
- Higher purity, carbon-added composite materials
- New products, such as zircon bricks for molten steel ladles were introduced
- Magnesia-carbon bricks for converters were introduced, becoming a mainstay in refractory materials
- Recycling of waste refractories was put into practice, reducing the environmental load
Limitless Growth
While refractory technology saw the biggest growth in the Industrial Revolution and in the years since WWII, there continue to be advancements and exciting innovations in the field.
Contact Us to learn more about the most cutting-edge refractories available.
The post A Brief History of Refractories appeared first on Refractory Materials, Precast Shapes, and Custom Solutions.
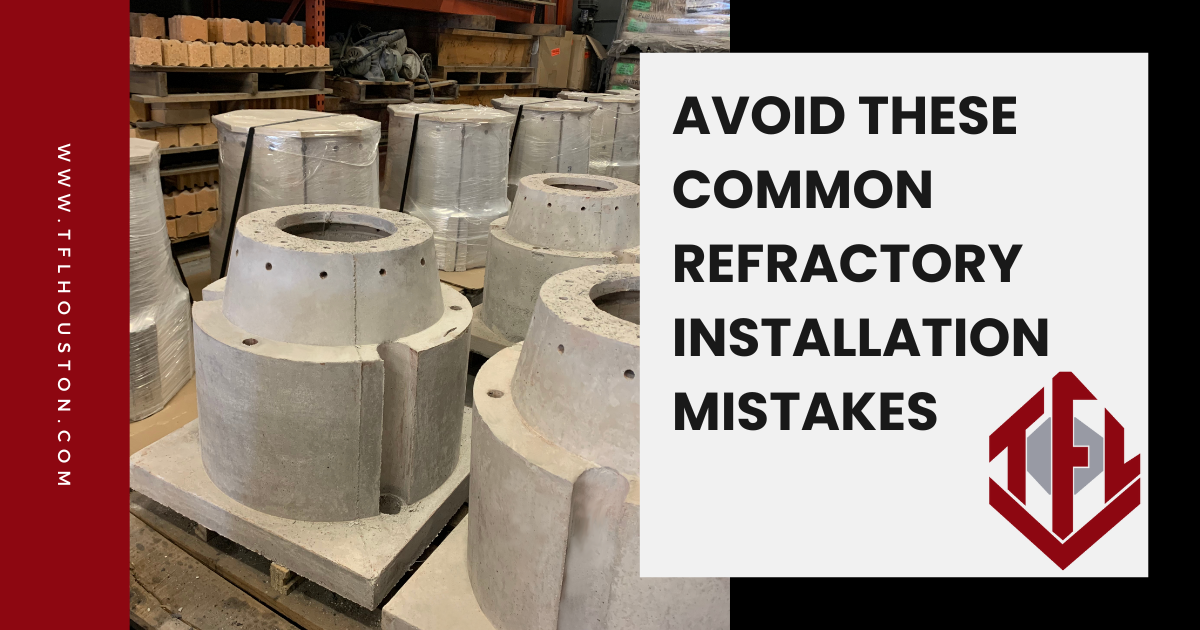
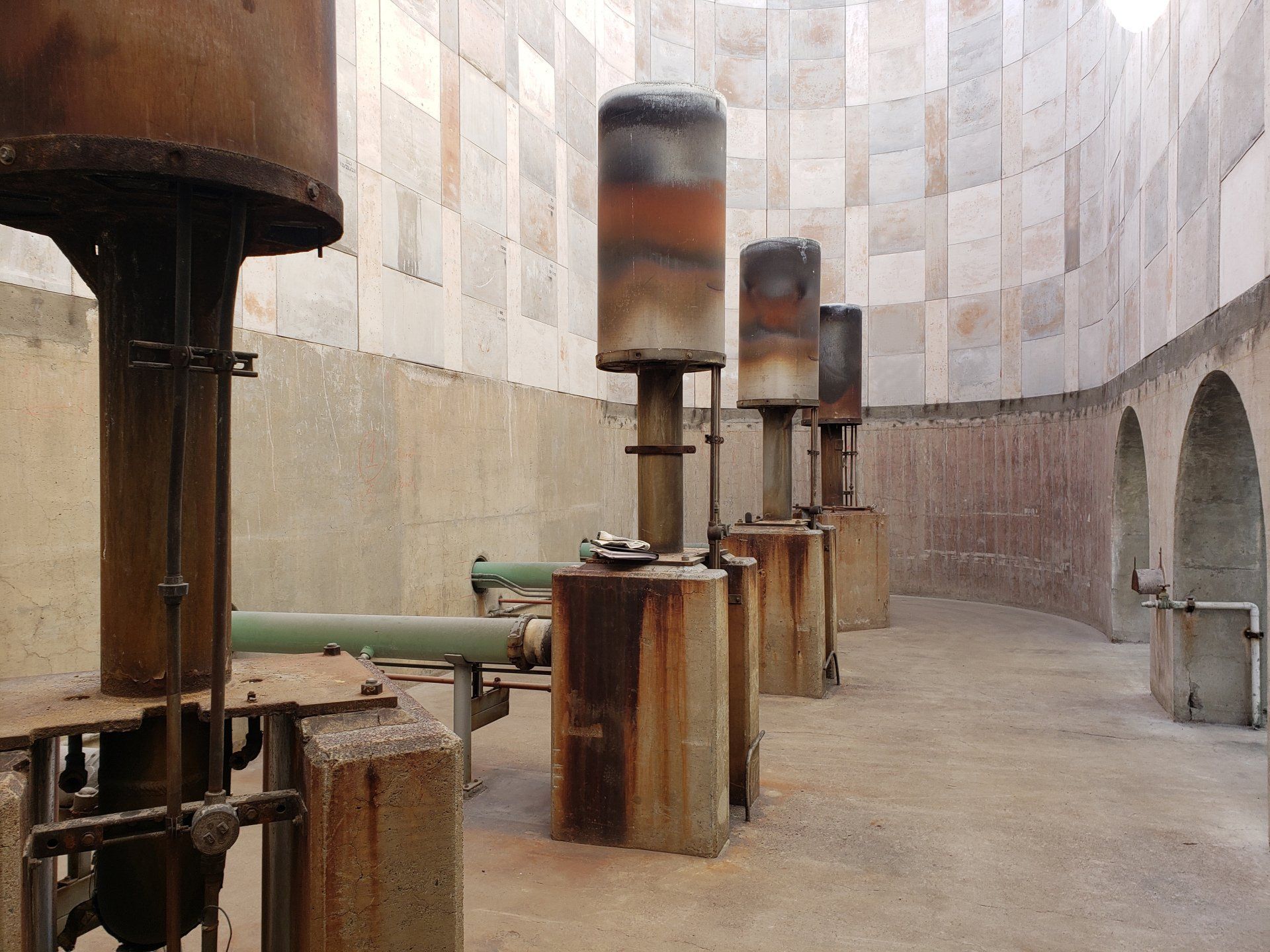
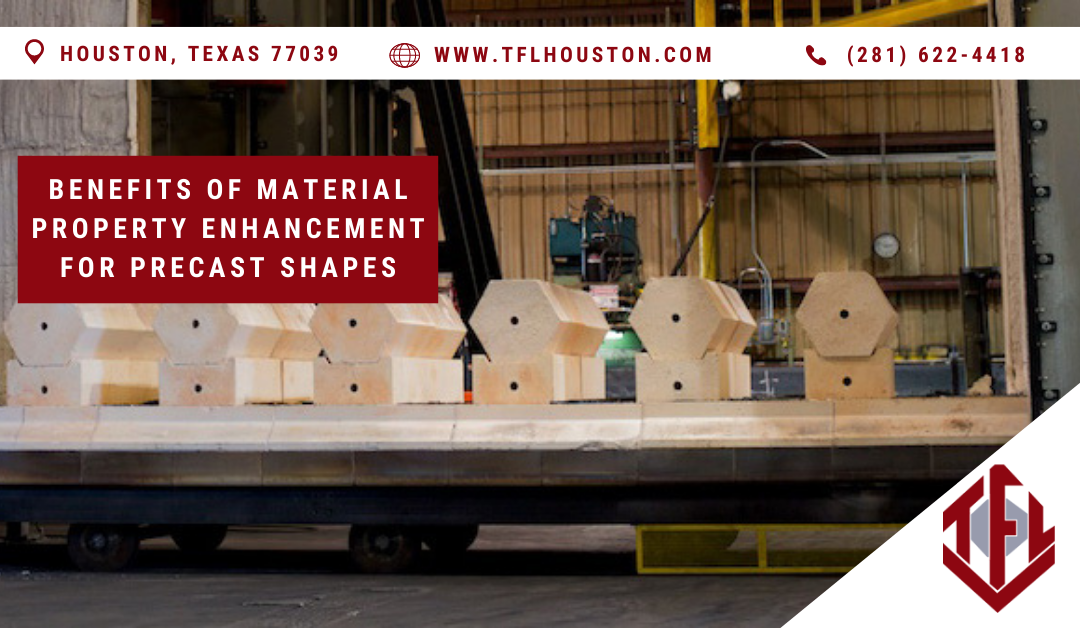
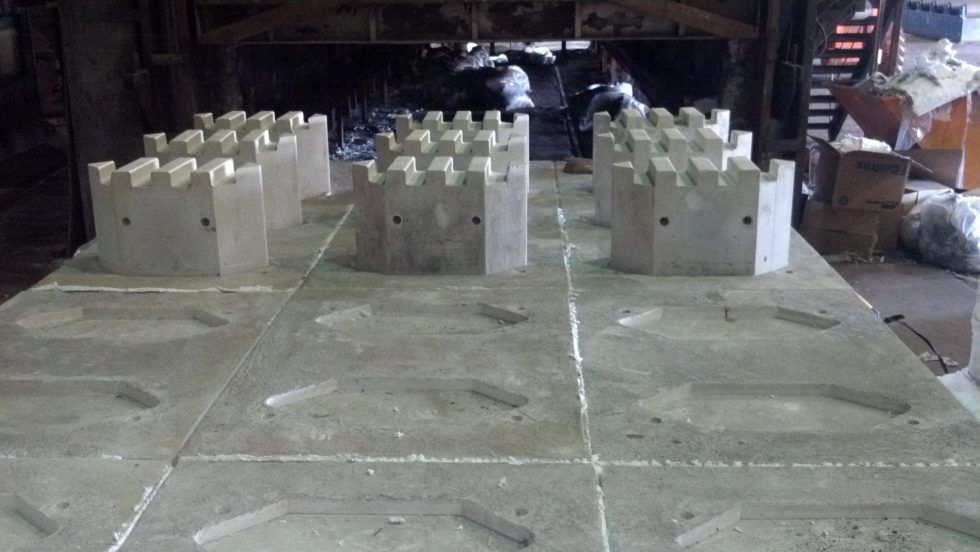
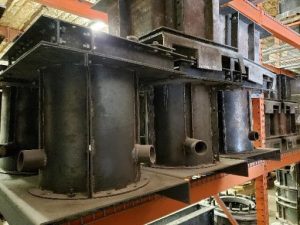
TFL Uses Custom Molding Techniques to Make Precast Refractory Shapes With Extremely Tight Tolerances
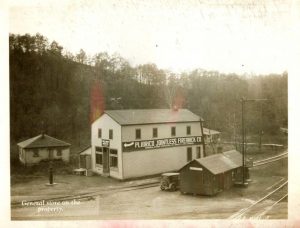