Top Benefits of Precast Refractory Shapes
Refractory repair can be a daunting, expensive process when you consider the downtime, demo, installation, and bake-out. With precast refractory shapes, much of that headache is eliminated.
Precast refractory shapes are consistent in composition, reliable in service and facilitate speedy repairs.
Click To Tweet
The Advantages of Precast Refractory Shapes
Refractory materials are generally divided into two kinds: precast (shaped refractories) and monolithic (unshaped refractories). Using precast refractory shapes has many advantages, including predictability, simplicity, and durability.
More Predictable
Physical properties of the material can be optimized if fired slowly, from all sides, through the entire thickness of the shape, not just the surface. The result is a truly homogeneous lining, uniform in nature and incredibly reliable. Since the intial firing is more controlled, there is also a reduction in m icro-cracking within the shape. In service, precast shape refractory linings see less stress and cracking, thanks to their independent nature.
Simplified Installation
Refractory installation contractors have come to consider precast refractory shapes much like any other pre-manufactured item, including insulation, ceramic fiber blanket and anchors. Precast shapes allow a bulk of refractory repair work to be completed prior to crews being on site, which can significantly reduce costs. This can give installation contractors a substantial advantage in competitive bid situations. In other installation methods such as guniting, as 45% more material is required to compensate for rebound and other loss. Using precast shapes requires significantly less material, translating to more savings.
Fast Bake-Out
An expensive and time-consuming aspect of refractory repair is the initial bake-out. The use of precast refractory shapes can reduce or even eliminate the need for an extensive bake-out. If all repairs are made with a prefired system, then normal furnace functioning can resume, without the fear of steam spalls or damage during initial heating. Bake-out of multi-component linings, which may include precast shapes and other materials,, can often be reduced by the pre-firing of the castable shapes.
Choosing the Right Material
The applications for precast shapes are virtually endless, with uses in a variety of different industries. Their use results in better performance, decreased downtime and significant cost savings. The successful design and manufacturing of high-performance refractories requires a thorough understanding of refractory materials, and no one knows them better than TFL.
Contact Us
today to find out more about REDI-SHAPEPrecast Shapes or our in-shop
precast shape fabrication
.
The post Top Benefits of Precast Refractory Shapes appeared first on Refractory Materials, Precast Shapes, and Custom Solutions.
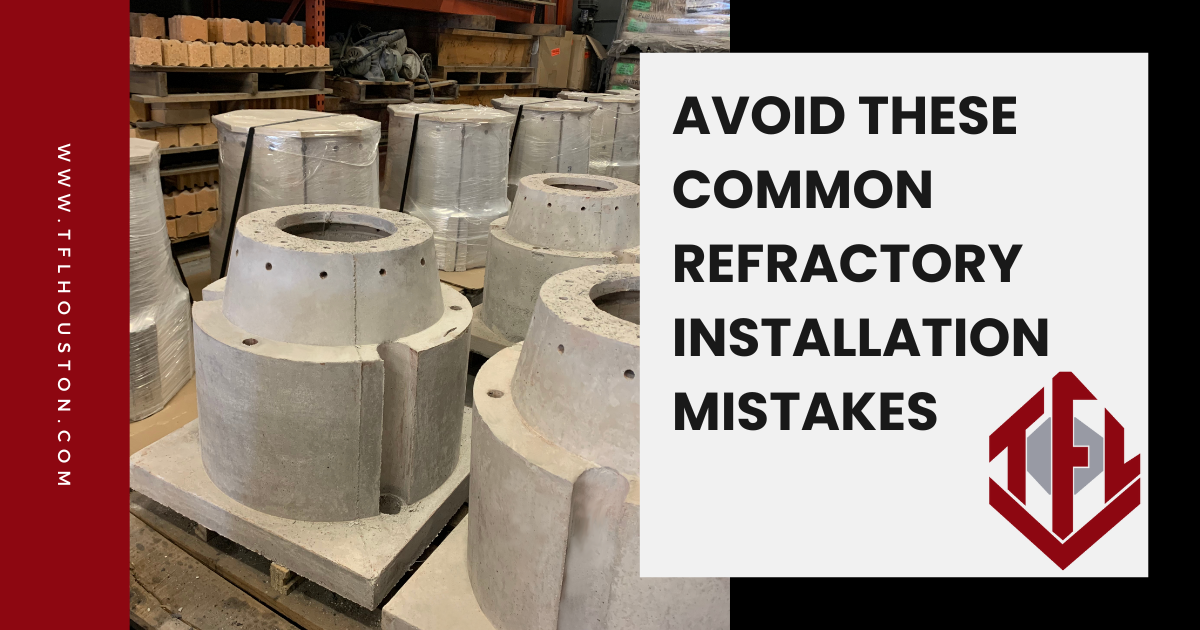
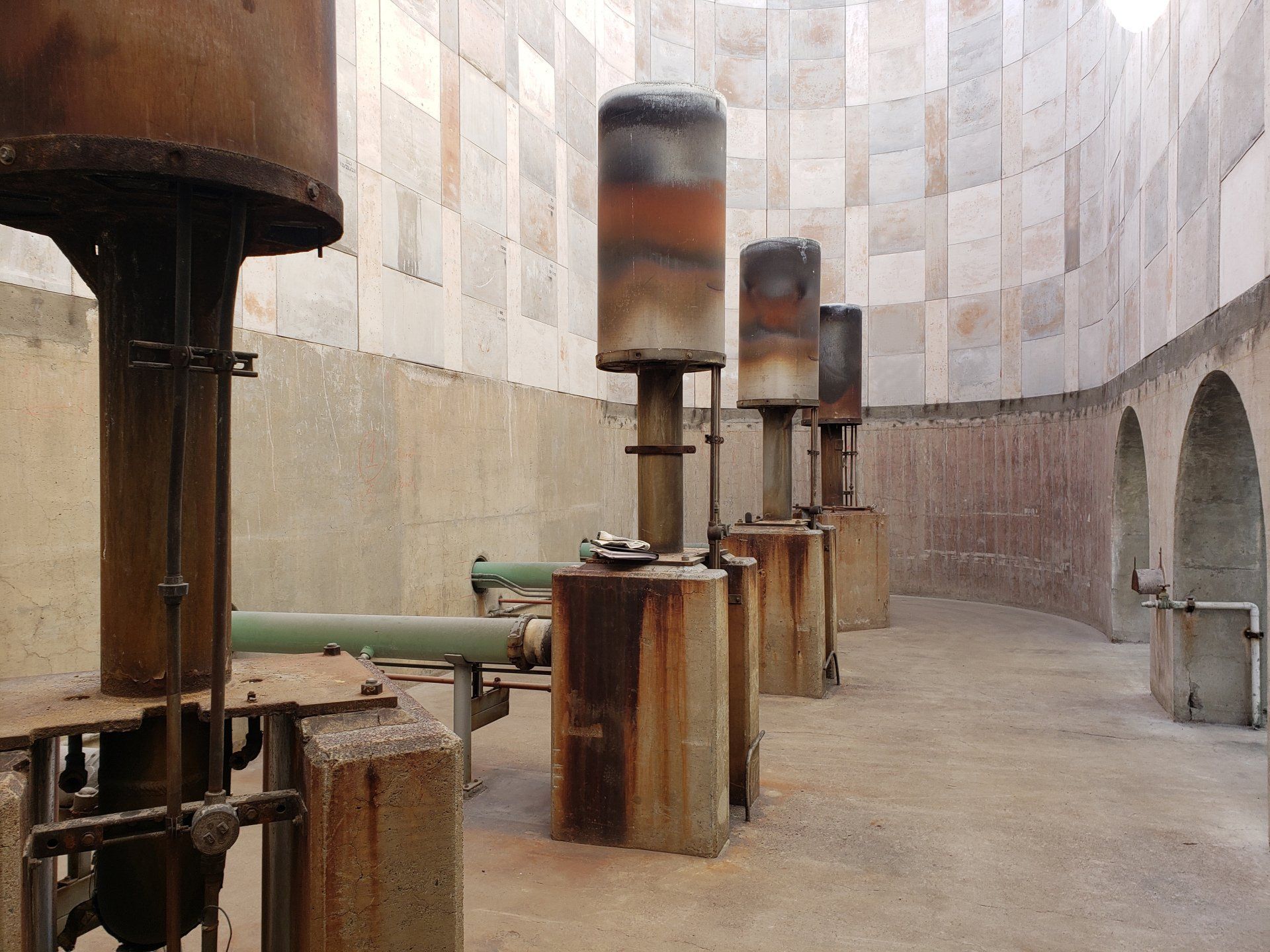
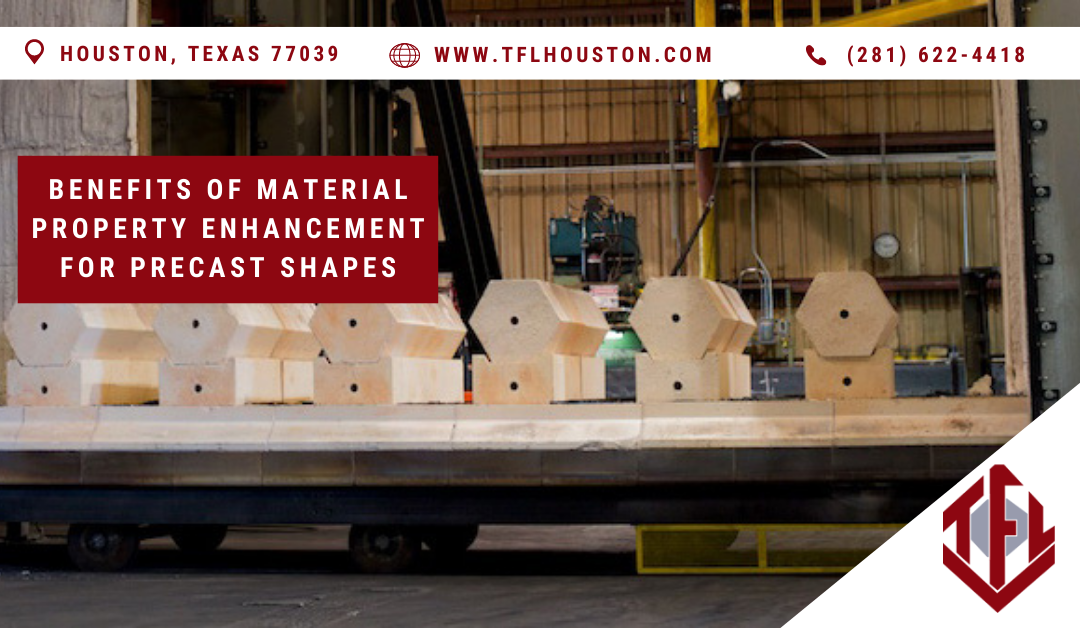
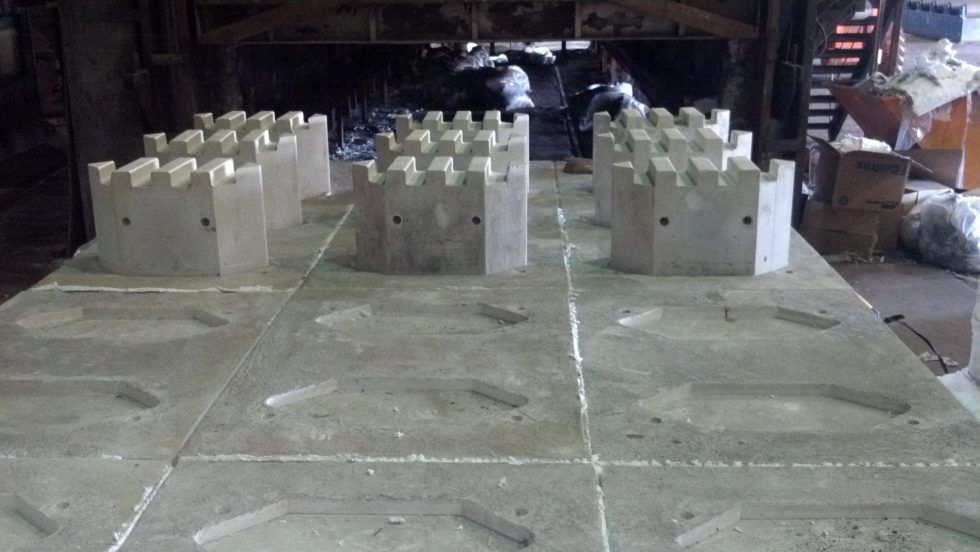
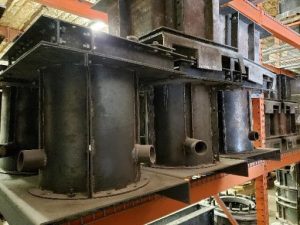
TFL Uses Custom Molding Techniques to Make Precast Refractory Shapes With Extremely Tight Tolerances
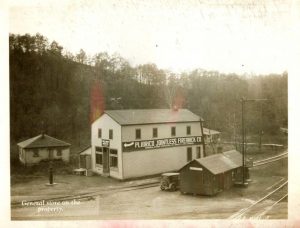