What are the Most Common Refractory Installation Mistakes?
Refractories are an admittedly complex product and an integral part of many industrial processes, but despite their importance, they are often seen almost as an afterthought by plant managers who don’t understand them. This presents a unique dilemma, as they will likely be tasked with selecting a refractory contractor to complete the crucial job of refractory installation.
If you’re planning a refractory installation job, watch for these common mistakes.
Click To Tweet
Common Refractory Installation Mistakes
Selecting and installing refractory lining materials is a process best suited for someone with accurate knowledge of the chemical and physical properties of the refractories and refractory materials, and the stresses these materials encounter during service. If the decision-maker lacks this kind of expertise, you may run into trouble. Here are some common installation mistakes made by inexperienced contractors:
Selecting the Wrong Materials
Choosing the best refractory materials is critical to protecting and maintaining the efficiency of your heat processing equipment, but it’s not always a priority for many industrial plant managers. However, modern refractory materials are engineered for specific applications that require specific placement techniques. Choosing the wrong material can sabotage your entire project.
Mixing Errors
When installing castable refractory, paying attention to the mixing process and keeping the consistency of each batch the same will help ensure that a proper refractory installation is off to a good start. Here are some common mixing errors encountered:
- Too much water was added during mixing
- The water used had impurities (was not potable)
- The wrong type of mixer was used
- The forms were prematurely removed before the material had been properly cured
Neglecting Dry Out
Dry out is the slow application of heat under controlled conditions to safely remove water from the refractory lining after the curing process is complete. Improper dry out can have devastating consequences for your refractory. If the time is cut too short in order to speed the commissioning of the unit, the refractory could experience damage before it’s even in use.
Pro Tip: If dry out time is cut short to get production back online, the refractory material could be significantly compromised.
Choosing the Wrong Installation Company
There is nothing simple or easy about a material that is expected to work under extreme conditions. While keeping costs down is an undeniable consideration, picking a well-trained and experienced installation company will ultimately ensure the success of your refractory lining installation.
An Often Overlooked But Critical Component
Though refractory linings are often an overlooked component on an industrial furnace or kiln, they are one of the most important for heat containment, energy efficiency, and proper operation of the industrial process. Consult with a competent refractory installer to achieve a better refractory installation, review the best practices, and avoid refractory failures.
Contact Us to learn more about refractory installation or to speak with a member of our team to find out how we can assist you with your refractory related needs.
The post What are the Most Common Refractory Installation Mistakes? appeared first on Refractory Materials, Precast Shapes, and Custom Solutions .
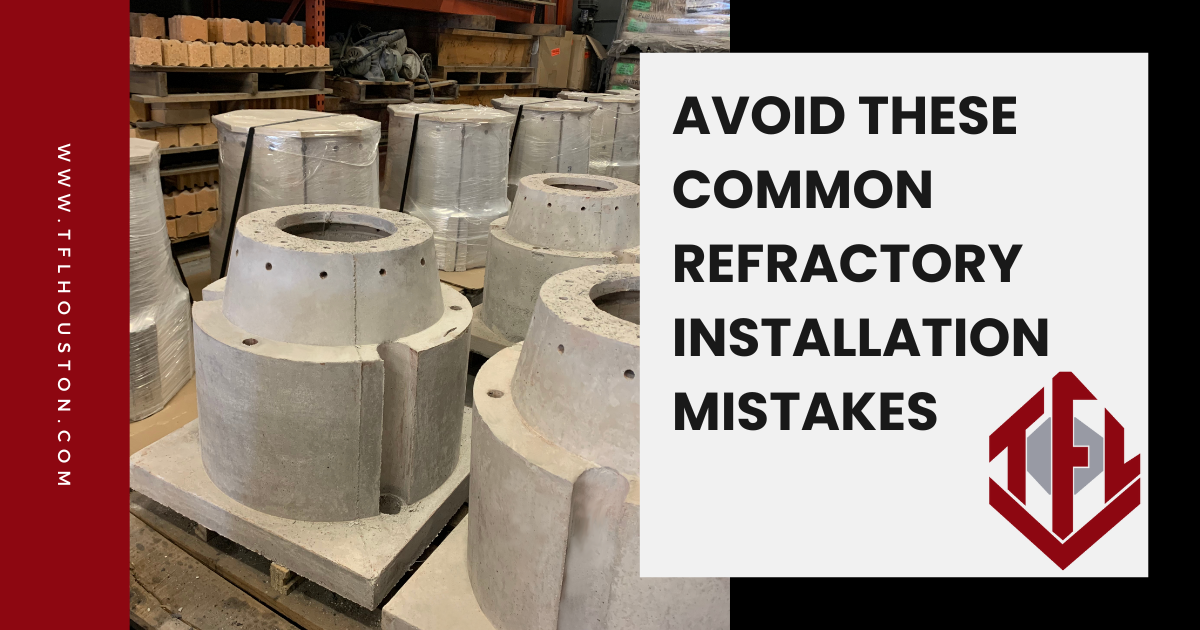
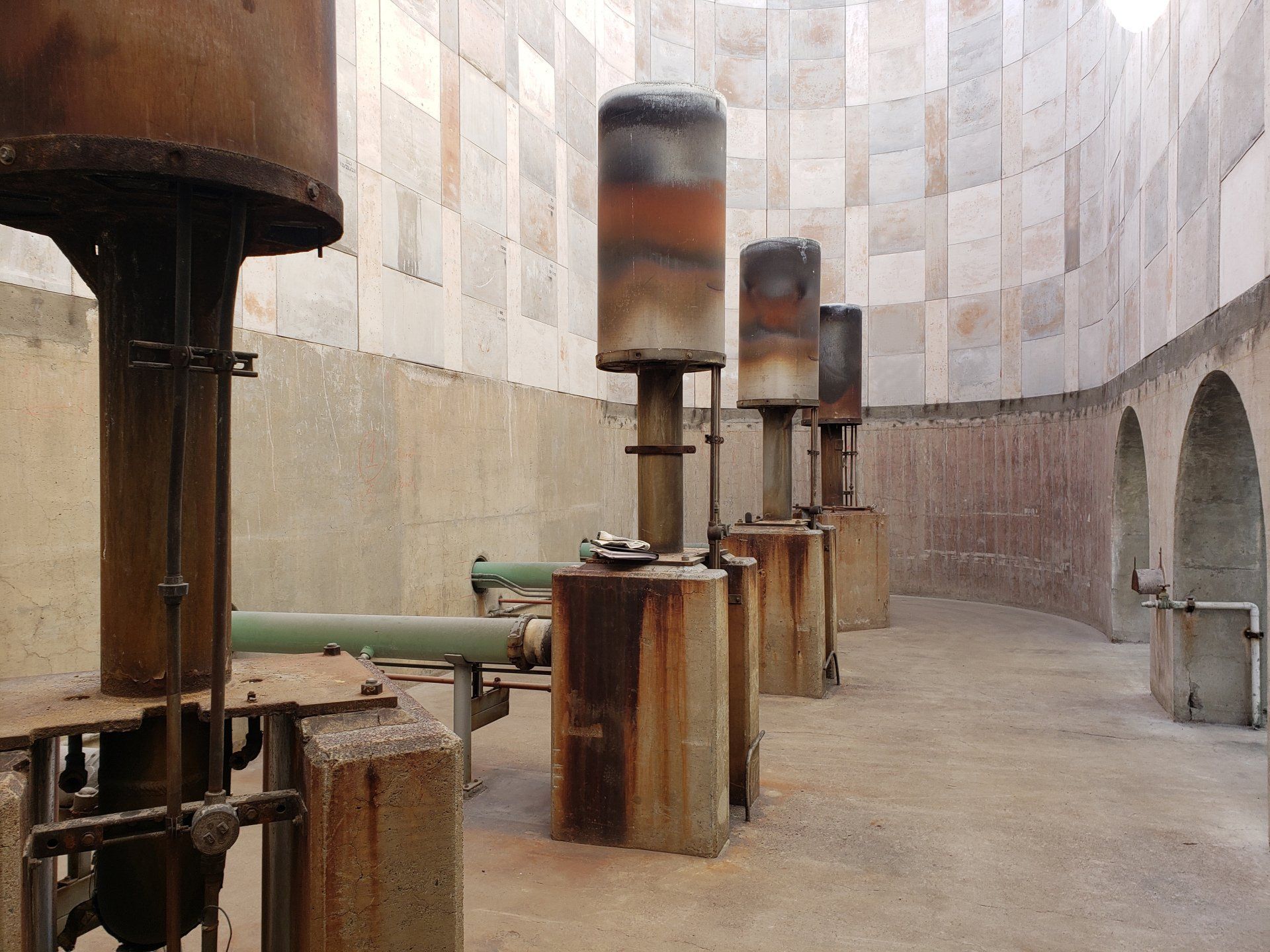
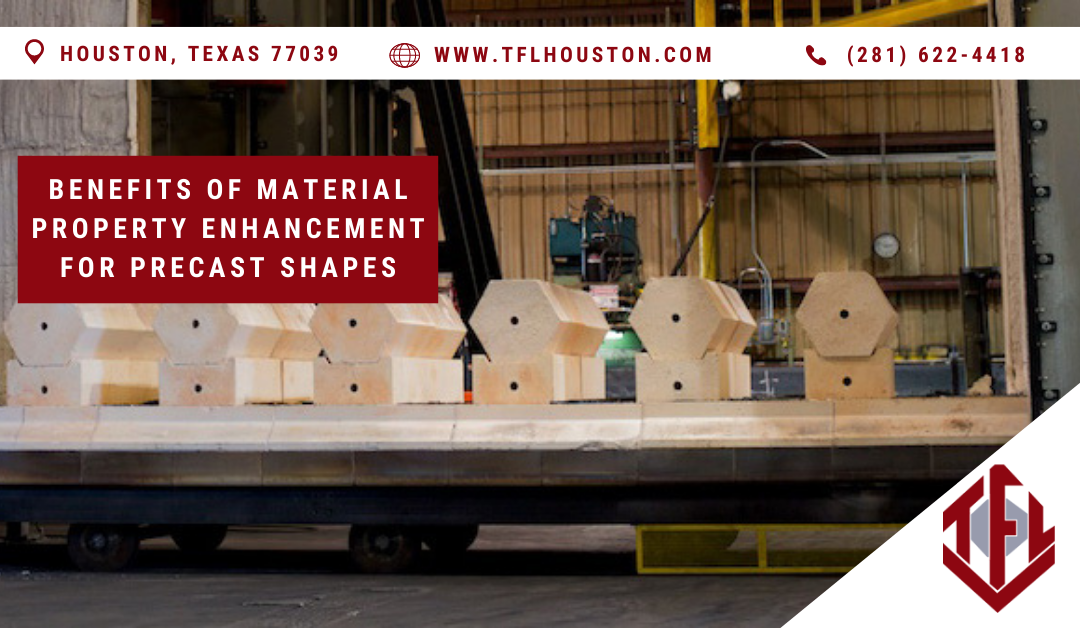
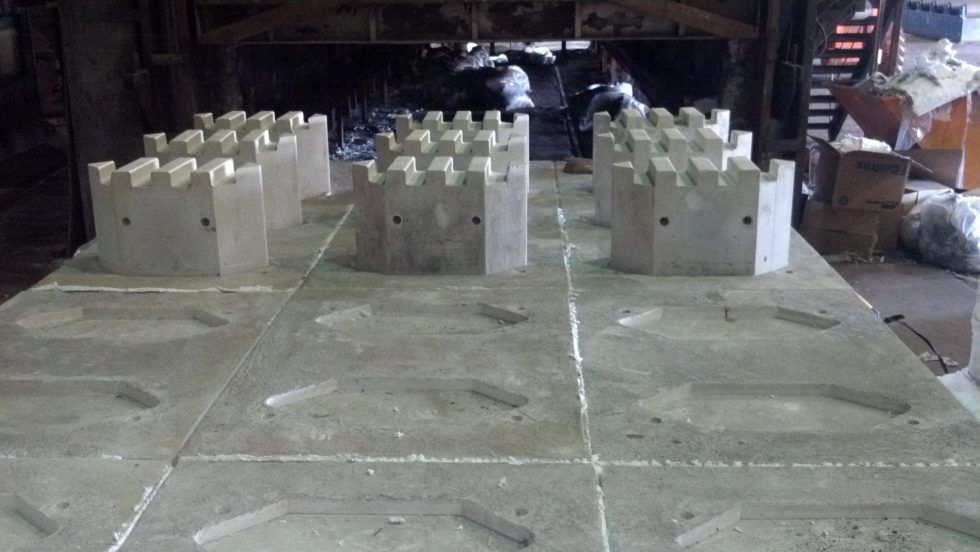
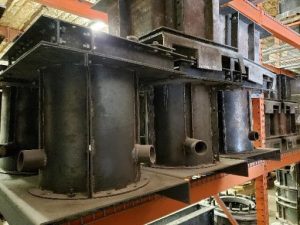
TFL Uses Custom Molding Techniques to Make Precast Refractory Shapes With Extremely Tight Tolerances
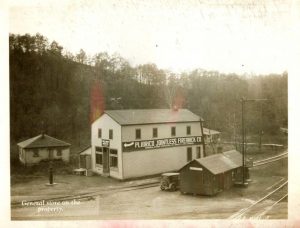