Key Considerations for Refractory Dry Out
With the pressure to perform comes the desire to push production levels and postpone necessary refractory repairs and maintenance, with very little consideration given to furnace heat up rates that could prevent damage to refractory linings. As a result, significant fluctuations in temperature have devastating effects on your refractory systems.
There are several key factors in refractory dry out that could affect your project. Learn how to address these challenges.
Click To Tweet
Curing & Dry Out
The curing process of a refractory cement takes place within the castable material after the dry material is mixed with water and either poured or guided into place. The water and refractory material then react to form a strong bond with the aggregate at ambient temperatures. This normally occurs in the first 24-48 hours after placement. Dryout is the initial application of heat under controlled rates to safely remove free and chemically combined water from the refractory lining after the curing process is complete. This may be the initial dry out after installation, or a subsequent dry out following repairs.
Budget
Budget constraints and economic restrictions are often the driving force behind inadequate or improper dry out. While your refractory might benefit from a slow, continuous ramp-rate dry out schedule if you did not plan for enough downtime the temptation to speed up the timeline might seem like a gamble worth taking.
ProTip: In environments that place tremendous pressure onto plant managers to reduce costs, minimize downtime and to get units operational, mistakes will be made.
Experience
For a new unit commissioning or a complete refractory system replacement, advanced planning for time and budgetary allowances is essential. Unfortunately, due to inexperienced engineers or contractors, these critical items may be missed in the project planning phase until very close to the intended startup date. This can lead to damage to the refractory before it is even able to perform.
Environment
Unit configuration and environmental considerations play an important part in planning for a proper dry out. This process entails more than just following a heating schedule. Issues such as burner sizing and location, exhaust location, air volume, and velocity, etc need to be addressed. The best dry out plan and schedule will fail if the unit environment isn’t factored in. For example, if you plan to use the main burner for dry out with no backup plan to use a third party burner/contractor to aide in the work, your process will grind to a halt if it’s discovered that the main burner is unable to do the dry out.
No Universal Dry Out Method
All dry out schedules should be developed with the specific unit to be dried out kept in mind. For castable linings, the refractory industry has typically utilized a ramp and hold regimen. Temperatures are ramped up at not to exceed rates (say 25°F – 75°F/hour) and then held at various hold points for specific periods of time. Even with this method, timelines and temperatures will vary, so it’s critical that you have an expert on your side.
Considerations for Refractory Dry Out
The combined efforts of an experienced refractory manufacturer, installer and dry out contractor result in optimal
refractory performance
. Do you have the best team for your refractory installation and dry out?
Contact Us
to learn more about proper refractory dry out, startup and shutdown.
The post Key Considerations for Refractory Dry Out appeared first on Refractory Materials, Precast Shapes, and Custom Solutions.
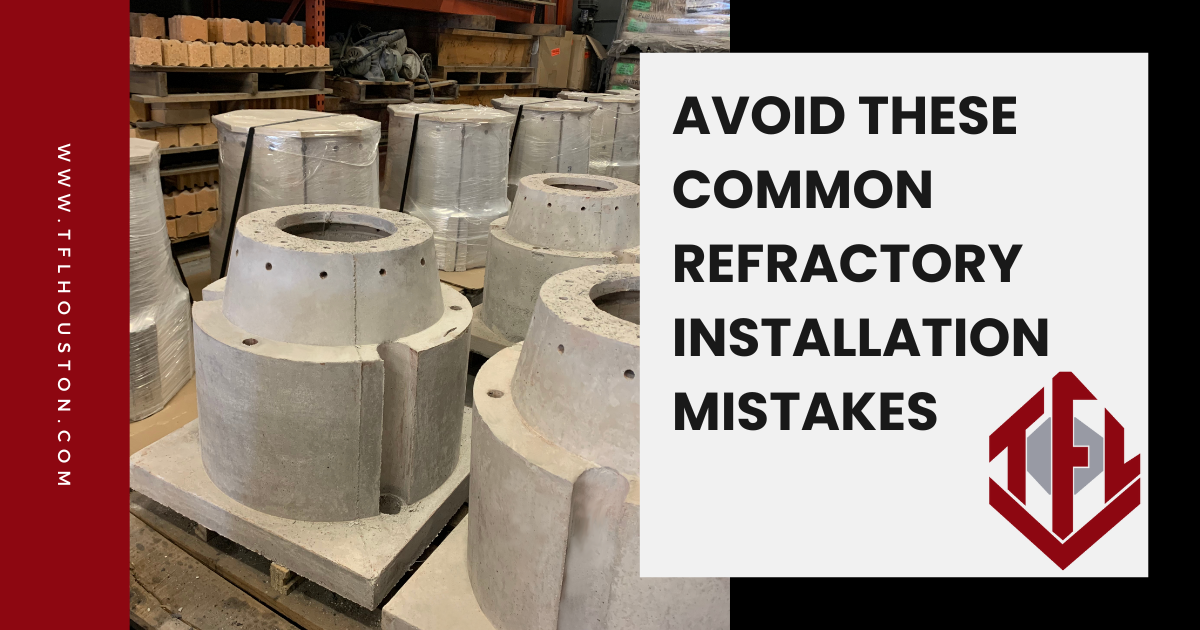
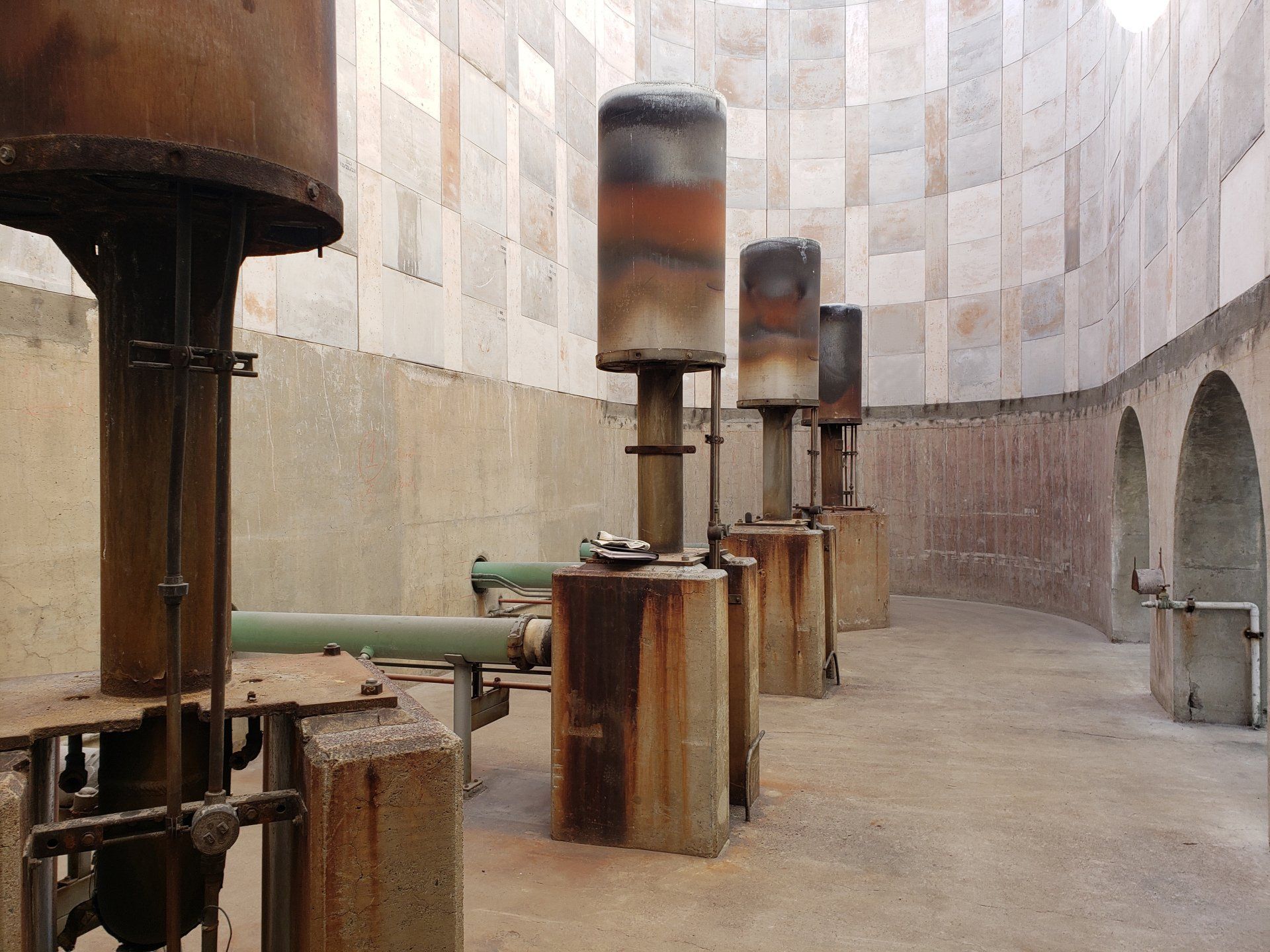
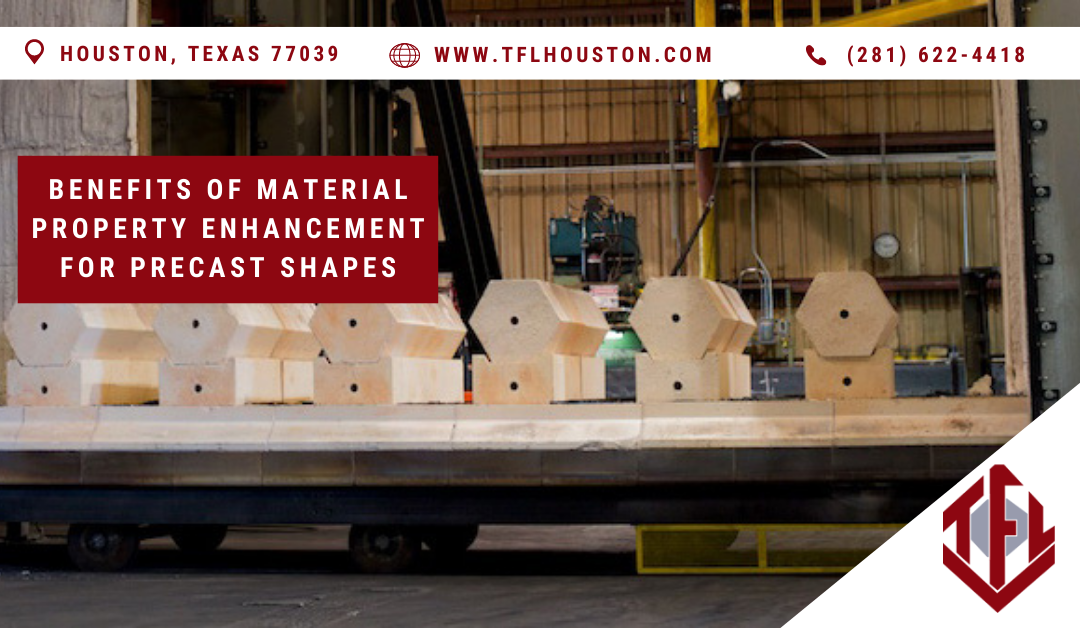
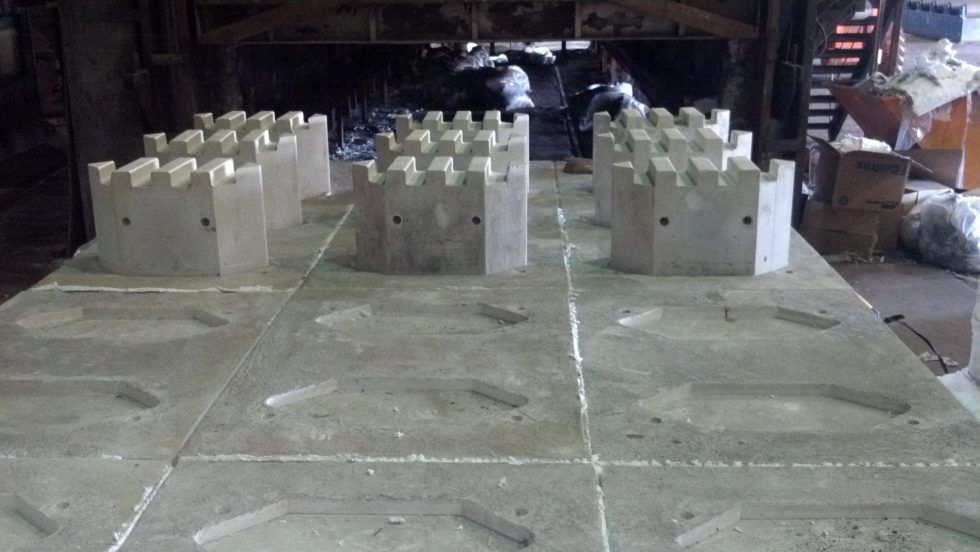
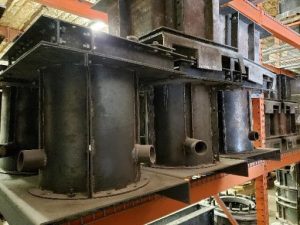
TFL Uses Custom Molding Techniques to Make Precast Refractory Shapes With Extremely Tight Tolerances
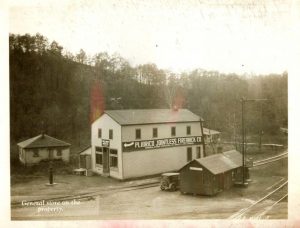