Refractory Tips: 5 Things Every Plant Manager Should Know
Refractories are a substantial investment, whether you’re managing a new construction or overseeing repair work. While refractory work might only be a small part of your construction project, the materials will protect your equipment, keep production online, and provide safety to your staff.
The cost of your refractory is far less than the value it will bring to your manufacturing plant.
Click To Tweet
Refractory Tips for Plant Managers
If refractory work is not the driving force of your plant, you may not have the level of expertise necessary to make decisions without help. Meeting with a reputable refractory expert can provide further insight and valuable advice. Here are 5 basic tips to help you in the meantime:
1) Refractories have different chemical compositions
- Acidic refractories aren’t affected by acids and consist of acidic materials such as silica, alumina and fire clay. They are adversely affected by basic materials.
- Neutral refractories are used when the slags need to be chemically stable to both acids and bases. Alumina, chromium, and carbon are often used in neutral refractories.
- Basic refractories are used where the slags are basic. These are stable to alkaline materials but could react with acids. Magnesia is ubiquitous to basic refractories.
2) Extreme heat isn’t the only threat to your refractory
Refractories must not only withstand extreme heat but must also be resistant to the chemicals that are released during the manufacturing process. If the wrong refractory is used, the chemical interaction between the refractory and byproducts of the materials being heated can cause catastrophic failure.
3) A small crack can be a big problem
Refractory inspection and repair should be a routine part of your refractory management plan. A very small crack can let enough heat out to disrupt the chemical process of the heated materials or can allow heat to burn the refractory fiber acting as insulation. The results can be devastating.
4) Installation matters
Correct refractory installation is crucial to the productivity of your plant and the safety of employees. Don’t forget that your refractory will need time to cure. Include this in your installation plan, and don’t try to rush it or cut corners!
5) Customization is key
Refractories aren’t one size fits all. Your plant may require custom refractory ingredient combinations explicitly created to provide the right protection for your application. Research and developments in the refractory industry have led to significant improvements and streamlining, but what works for one doesn’t work for all.
The Best Results
Whatever the size of your production facility, we can guide you through the process and show you how to find the best solution for your refractory application. You should never go into the process without an expert on your side.
Contact Us to learn more about choosing the right refractory for the job.
The post Refractory Tips: 5 Things Every Plant Manager Should Know appeared first on Refractory Materials, Precast Shapes, and Custom Solutions.
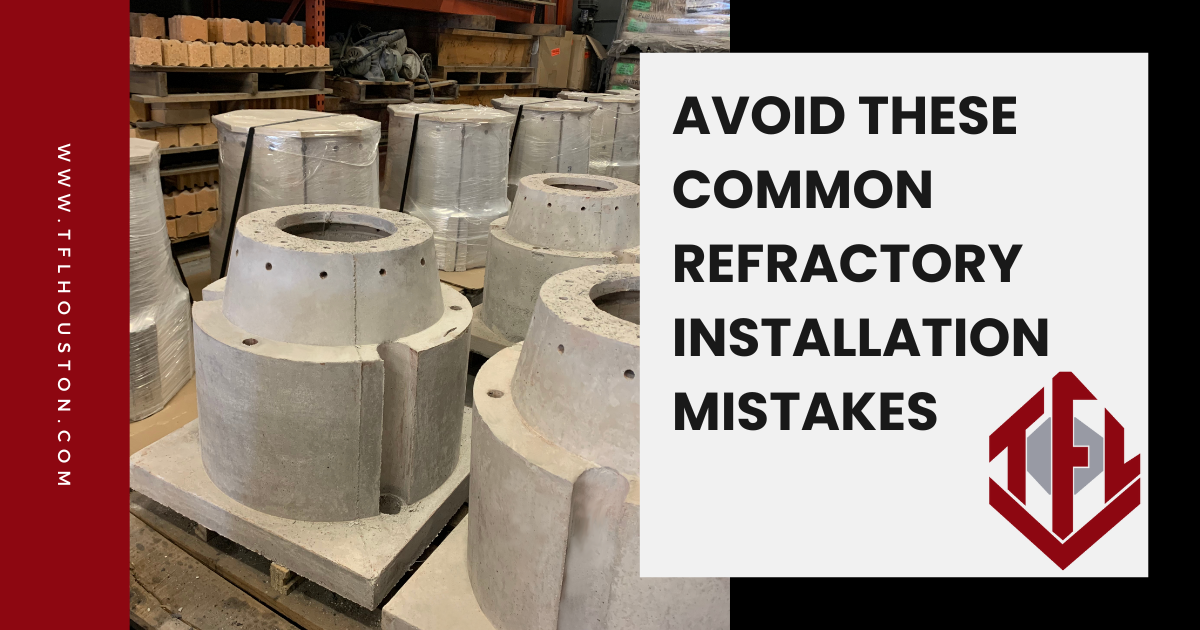
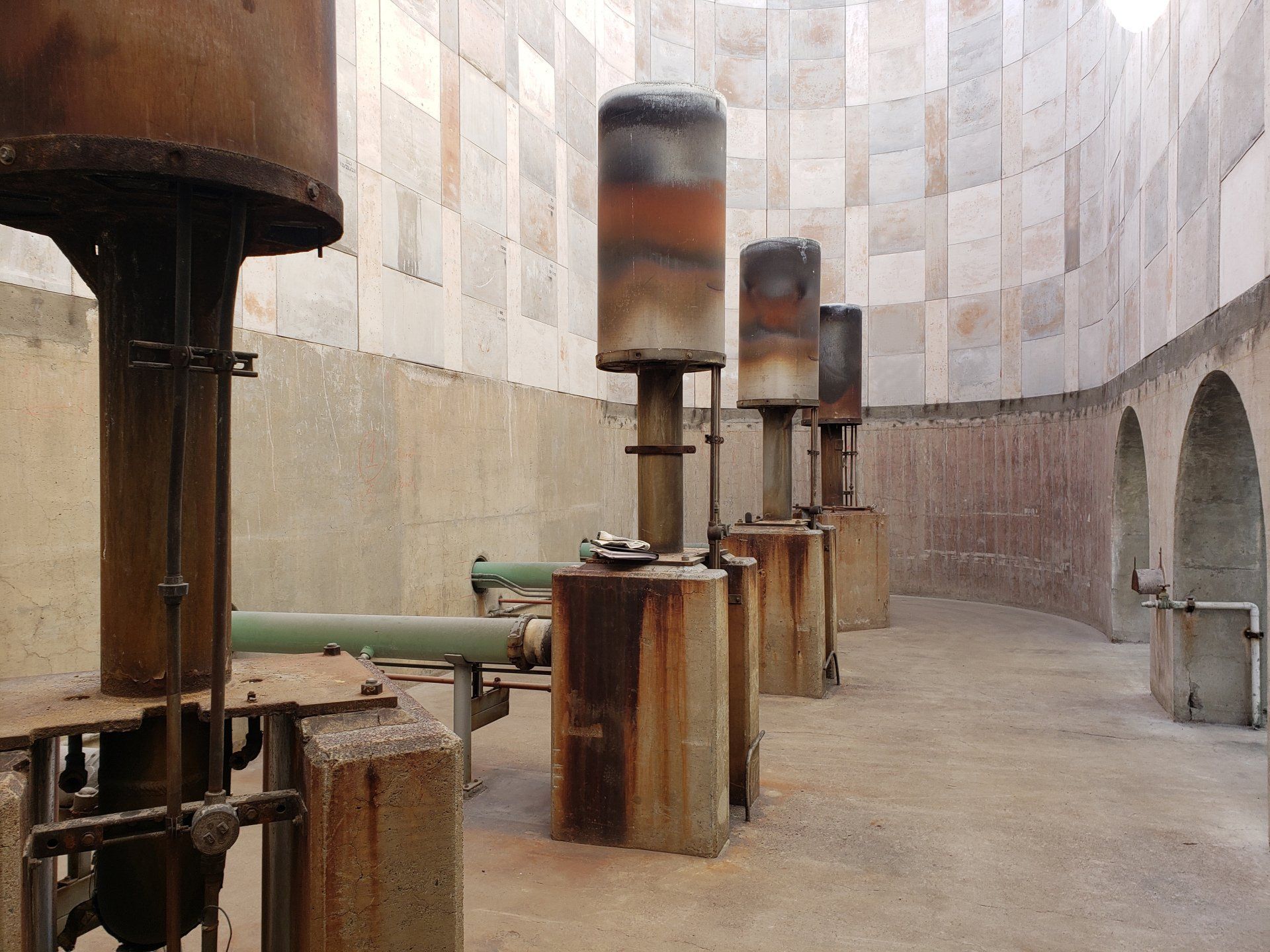
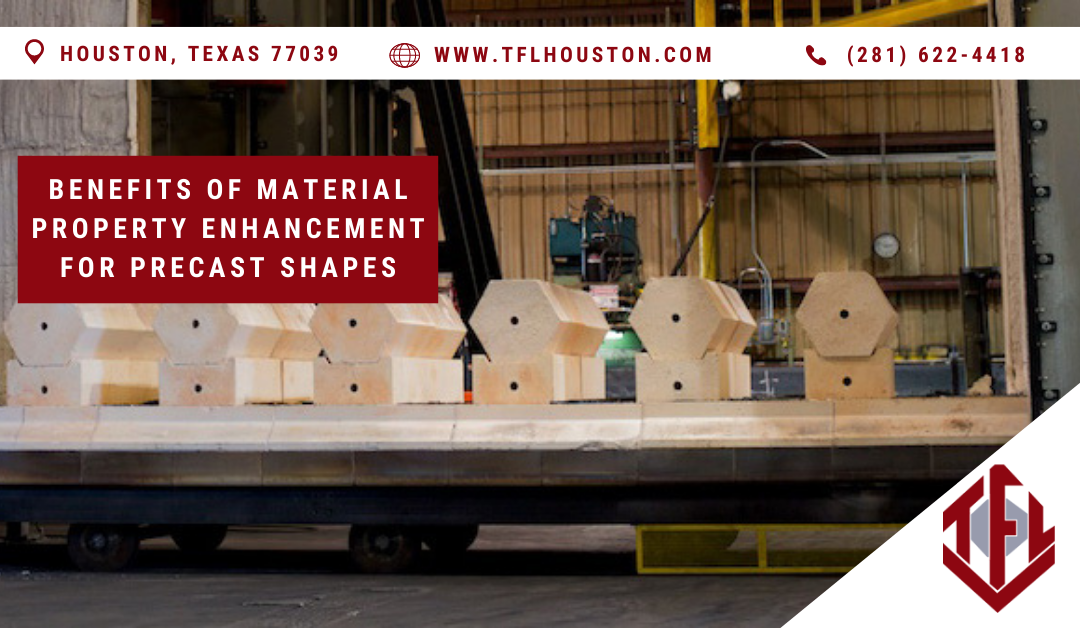
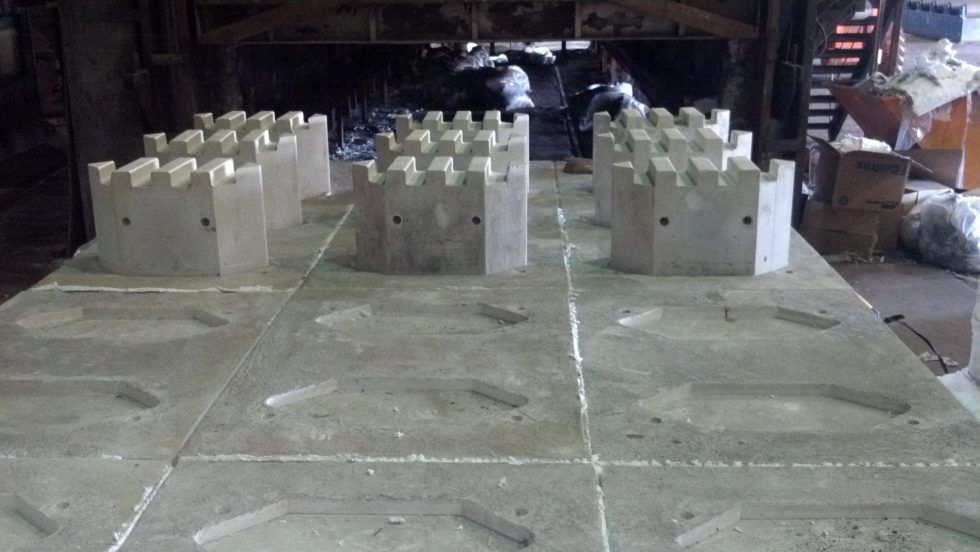
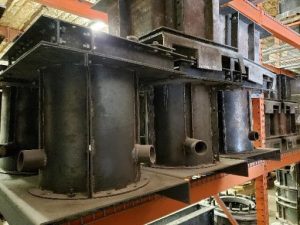
TFL Uses Custom Molding Techniques to Make Precast Refractory Shapes With Extremely Tight Tolerances
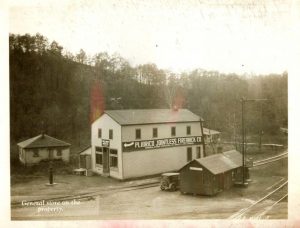