Choosing a Monolithic Refractory Installation Method
Choosing the best refractory material can be overwhelming by itself, but that’s only half the battle. You also need to select the right installation method and get a team with the experience and skill to get the job done right.
How should you choose the right refractory installation method? Use this guide to help you along the way.
Click To Tweet
Monolithic Refractory Installation
Technology has advanced to make the installation of refractories more cost-effective. Consider the refractory lining, which is a protective layer inside the kiln or furnace. The lining acts as a form of insulation to withstand high temperatures, and also helps protects the structure from thermal shock and abrasion. Here’s a summary of the best ways to install monolithic refractory linings:
- Shotcrete
- Gunite
- Ramming
- Casting
1) Shotcrete
Shotcrete is typically a low-cement, low-moisture refractory that is fully tempered and mixed with water and special binding additives, and then projected at high velocity onto a surface.
2) Gunite
Gunite is a dry monolithic refractory designed for use with dry gunning equipment. It uses compressed air to send the dry material to the nozzle, where it mixes with water. Then it sprays out at super high velocity, which compacts the material on placement.
3) Ramming
Ramming plastics or castables are versions modified such that they can be hand-rammed into place. Lining-support fittings are attached to the shell (metal anchors or ceramics tile anchors for the wall). The material is quite literally rammed into place using a pneumatic hand hammer. Forms may or may not be used, depending on the situation.
4) Casting
Casting refers to pouring wet castables into forms. Castables can be molded by hand or poured into forms to achieve whatever shape is desired. Once hydration of the cement in the mix is complete, the forms are removed.
Pro Tip: Each refractory installation method has pros and cons, but the risks can be mitigated by hiring an experienced installation team and using top quality materials.
Choosing an Installation Method
Proper refractory installation is vital to achieving a quality refractory lining. Choosing the right installation method comes down to several factors, including:
- Budget: Even when the price doesn’t vary much between materials, installation methods that lead to more waste will generally end up costing you more.
- Site Conditions: Is the site at a high elevation? Will you be able to set up near the work site? Will you need to stop and start several times?
- Volume: Gunite and shotcrete methods deliver high volumes in a short amount of time (upwards of 5 tons per hour), so you must be prepared to handle that in your installation planning.
- Installation Team’s Skill Level: Whether shotcreting, guniting, ramming or casting, an inexperienced crew can directly affect the amount of refractory material waste, and therefore the total job cost.
- Bakeout: Different refractories have different bakeout times and these should be considered in your project schedule.
Partner With an Expert
There’s no universal method for installing monolithic refractory linings, but if you do your research and partner with a refractory expert, you’ll be more likely to choose the best method for your specific requirements. Remember that using top quality refractory materials, like Plibrico , will further set you up for success.
Contact Us to learn more about refractory installation methods.
The post Choosing a Monolithic Refractory Installation Method appeared first on Refractory Materials, Precast Shapes, and Custom Solutions.
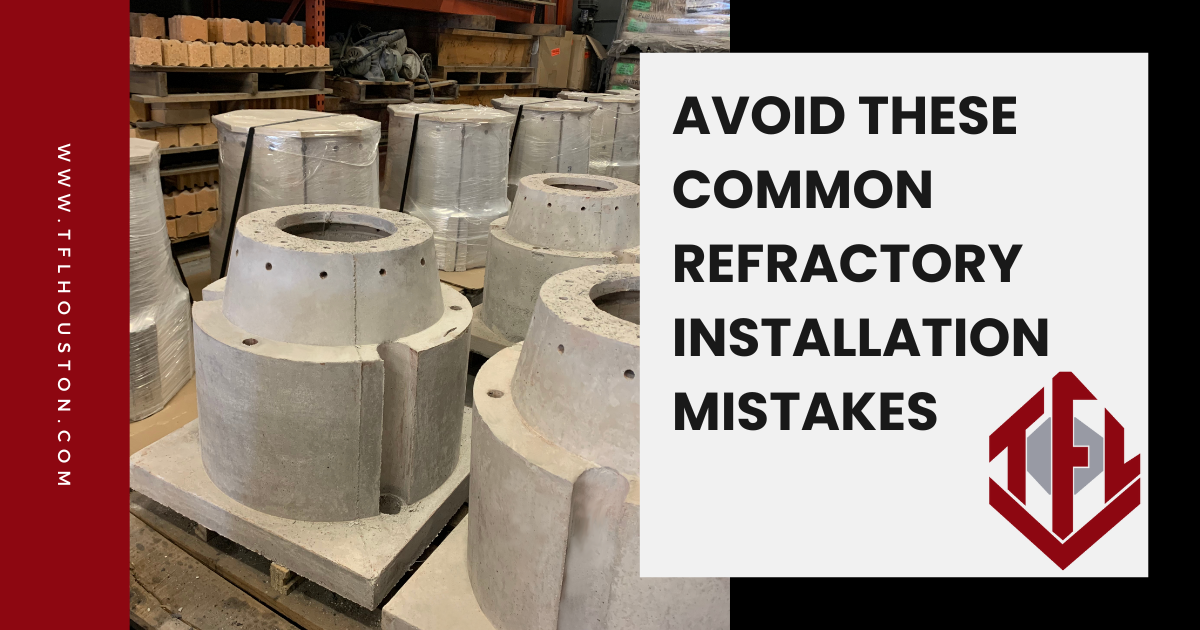
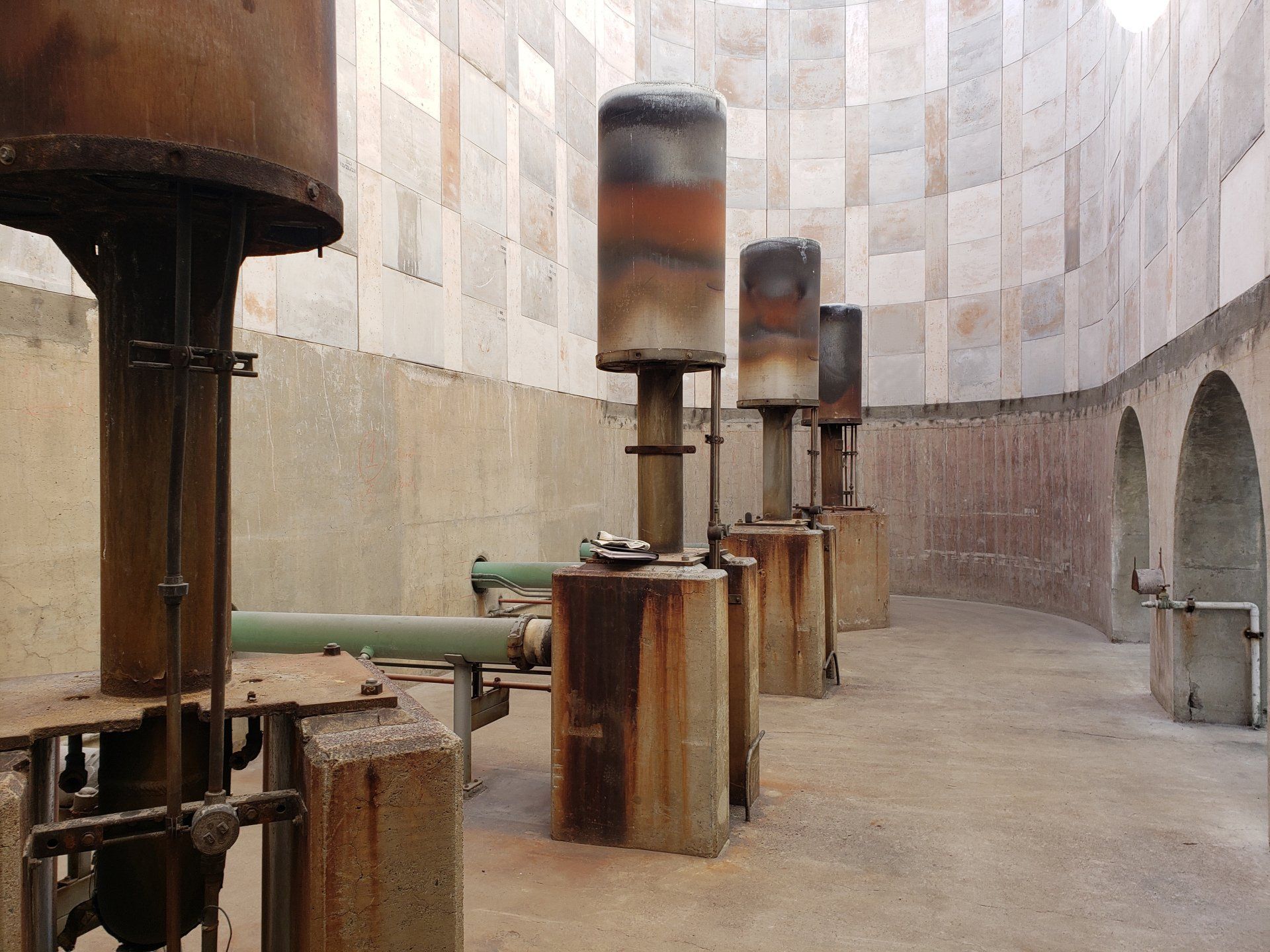
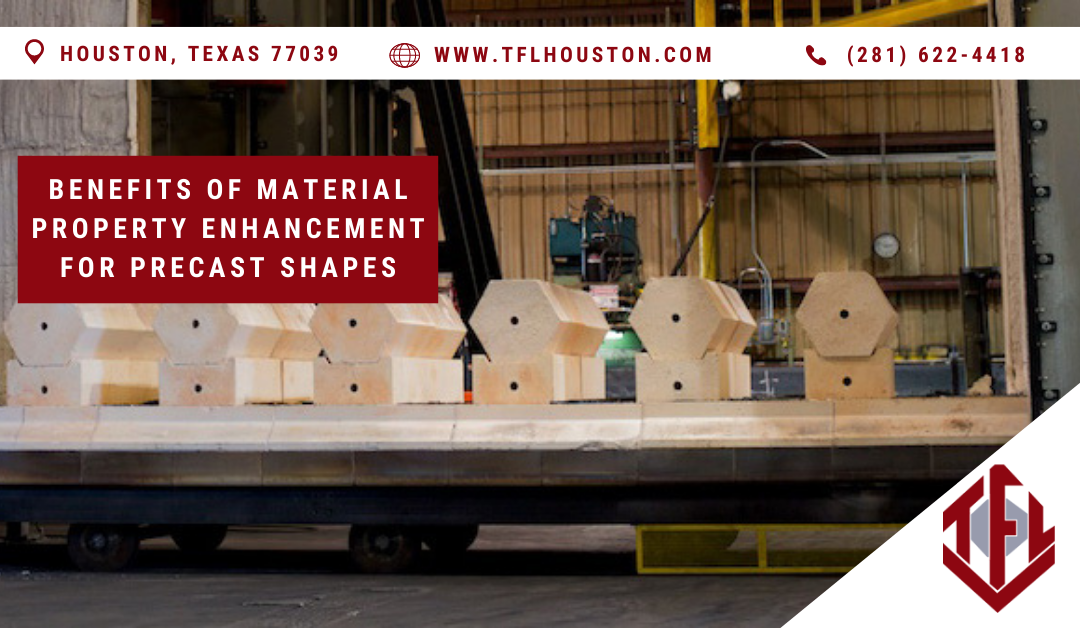
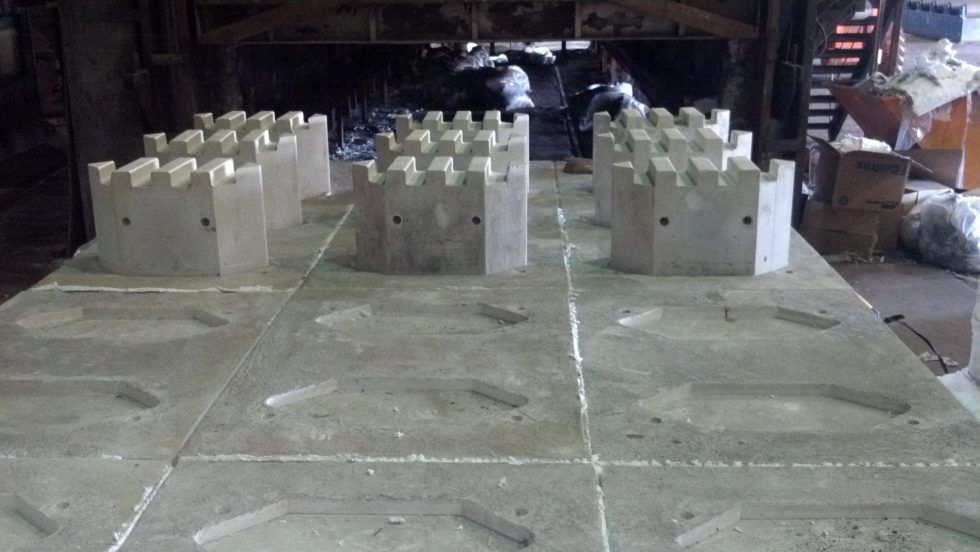
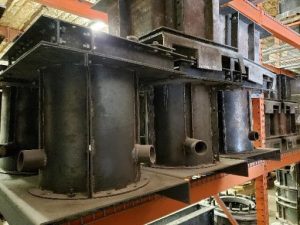
TFL Uses Custom Molding Techniques to Make Precast Refractory Shapes With Extremely Tight Tolerances
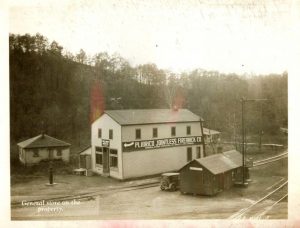